Method for leaching zinc from purification copper, cadmium, cobalt and nickel slag of zinc hydrometallurgy
A technology for hydrometallurgical zinc smelting and copper purification, applied in the field of zinc leaching, can solve the problems of long leaching time and low zinc recovery rate, and achieve the effects of low treatment cost, high leaching rate and simple process
- Summary
- Abstract
- Description
- Claims
- Application Information
AI Technical Summary
Problems solved by technology
Method used
Examples
Embodiment 1
[0021] Take 1000g of purified copper, cadmium, cobalt and nickel slag containing 49.10wt% of zinc, the particle size is less than 2mm, and the pulp concentration is 50%, and the ball mill is used for grinding, the ball mill speed is 25r / min, and the grinding time is 5min, and then the purified copper after grinding is obtained. Cadmium cobalt nickel slag slurry;
[0022] The leaching condition of purified copper cadmium cobalt nickel slag slurry after grinding is: temperature 40 o C, the liquid-solid ratio is 3.7:1, adding concentration is 20wt% sulfuric acid to make the terminal pH of leaching solution be 3.30, reaction time 60min, the consumption of potassium permanganate is 0.017 times of purifying copper-cadmium-cobalt-nickel slag quality, agitator speed 300r / min, followed by solid-liquid separation to obtain a zinc-containing leaching solution. The zinc leaching rate of this embodiment is 99.32%, and the zinc concentration in the leach solution is 131.80g / L.
Embodiment 2
[0024] Take 1000g of purified copper, cadmium, cobalt, and nickel slag containing 51.89wt% of zinc, the particle size is less than 2mm, and the pulp concentration is 45%, and the ball mill is used for grinding. The ball mill speed is 25r / min, and the grinding time is 10min, and then the purified copper after grinding is obtained. Cadmium cobalt nickel slag slurry;
[0025] The leaching conditions of the purified copper cadmium cobalt nickel slag slurry after grinding are: temperature 85 o C, the liquid-solid ratio is 4.0:1, adding a concentration of 20wt% sulfuric acid to make the final pH of the leaching solution 3.00, the reaction time is 75min, the amount of potassium permanganate is 0.020 times the quality of the purified copper-cadmium-cobalt-nickel slag, and the stirring speed is 600r / min, followed by solid-liquid separation to obtain a zinc-containing leaching solution. The zinc leaching rate of this embodiment is 99.11%, and the zinc concentration in the leach soluti...
Embodiment 3
[0027] Take 1000g of purified copper, cadmium, cobalt and nickel slag containing 45.37wt% of zinc, the particle size is less than 2mm, and the pulp concentration is 50%, and the ball mill is used for grinding, the ball mill speed is 25r / min, and the grinding time is 5min, and then the purified copper after grinding is obtained. Cadmium cobalt nickel slag slurry;
[0028] The leaching condition of purified copper cadmium cobalt nickel slag slurry after grinding is: temperature 65 o C, the liquid-solid ratio is 3.5:1, the concentration of adding sulfuric acid is 20wt% so that the end point pH of the leachate is 3.50, the reaction time is 90min, the amount of potassium permanganate is 0.015 times of the quality of the purified copper cadmium cobalt nickel slag, and the stirring speed is 450r / min, followed by solid-liquid separation to obtain zinc-containing leaching solution and leaching residue. The zinc leaching rate of this embodiment is 99.20%, and the zinc concentration in...
PUM
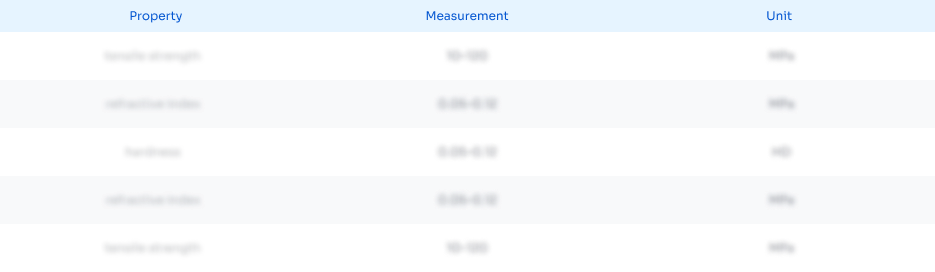
Abstract
Description
Claims
Application Information

- R&D Engineer
- R&D Manager
- IP Professional
- Industry Leading Data Capabilities
- Powerful AI technology
- Patent DNA Extraction
Browse by: Latest US Patents, China's latest patents, Technical Efficacy Thesaurus, Application Domain, Technology Topic, Popular Technical Reports.
© 2024 PatSnap. All rights reserved.Legal|Privacy policy|Modern Slavery Act Transparency Statement|Sitemap|About US| Contact US: help@patsnap.com