Composite silk textile material and preparation method thereof
A technology of textile materials and silk, which is applied in the manufacture of rayon, textiles and paper, conjugated rayon, etc., can solve the problems of corrosion resistance and lack of durability, and achieve improved air permeability, strong practicability and cheap raw materials. Effect
- Summary
- Abstract
- Description
- Claims
- Application Information
AI Technical Summary
Problems solved by technology
Method used
Image
Examples
Embodiment 1
[0026] (1) Weigh 15 parts of hollow fiber, 15 parts of viscose fiber, 15 parts of cellulose acetate, 15 parts of carboxymethyl cellulose, 20 parts of silk fiber, 5 parts of coconut fiber, 5 parts of xanthan gum, sorbitol 5 parts, 5 parts of sodium alginate, 5 parts of ceteareth, 5 parts of 2-chlorohydrochloric acid, 5 parts of sulfur hexafluoride, 2-hydroxy-4-methoxy-5-sulfonic acid diphenylmethyl 2 parts of ketone, 2 parts of 4-methoxyphenol, 2 parts of sorbitan monolaurate, 5 parts of potassium sodium tartrate tetrahydrate and 5 parts of magnesium diisopropylamide;
[0027] (2) Mix hollow fiber, viscose fiber, cellulose acetate and carboxymethyl cellulose into 30% ethanol solution, keep warm and activate for 1 hour, and keep warm at 30°C;
[0028] (3) Mix silk fiber, coconut fiber, xanthan gum, sorbitol and sodium alginate into 5% boric acid solution, use ultrasonic pulverizer, ultrasonic pulverize for 60 minutes, the power of ultrasonic pulverizer is 150W;
[0029] ...
Embodiment 2
[0035] (1) Weigh 20 parts of hollow fiber, 20 parts of viscose fiber, 20 parts of acetate fiber, 20 parts of carboxymethyl cellulose, 25 parts of silk fiber, 8 parts of coconut fiber, 8 parts of xanthan gum, sorbitol 8 parts, 8 parts of sodium alginate, 8 parts of ceteareth, 8 parts of 2-chlorohydrochloric acid, 8 parts of sulfur hexafluoride, 2-hydroxy-4-methoxy-5-sulfonic acid diphenylmethyl 3 parts of ketone, 3 parts of 4-methoxyphenol, 3 parts of sorbitan monolaurate, 6 parts of 5-sulfosalicylic acid dihydrate and 6 parts of ethyl potassium bromide;
[0036] (2) Mix hollow fiber, viscose fiber, acetate fiber and carboxymethyl cellulose into 30% ethanol solution, keep warm and activate for 1.2 hours, and keep warm at 35°C;
[0037] (3) Mix silk fiber, coconut fiber, xanthan gum, sorbitol and sodium alginate into a 5% boric acid solution, use an ultrasonic pulverizer, ultrasonic pulverize for 70 minutes, and the power of the supersonic pulverizer is 180W;
[0038] (...
Embodiment 3
[0044] (1) Weigh 30 parts of hollow fiber, 30 parts of viscose fiber, 30 parts of acetate fiber, 30 parts of carboxymethyl cellulose, 35 parts of silk fiber, 10 parts of coconut fiber, 8 parts of xanthan gum, sorbitol 8 parts, 8 parts of sodium alginate, 8 parts of ceteareth, 8 parts of 2-chlorohydrochloric acid, 8 parts of sulfur hexafluoride, 2-hydroxy-4-methoxy-5-sulfonic acid diphenylmethyl 4 parts of ketone, 4 parts of 4-methoxyphenol, 4 parts of sorbitan monolaurate, 8 parts of trisodium citrate dihydrate and 8 parts of diisobutyl sodium hydride;
[0045] (2) Mix hollow fiber, viscose fiber, acetate fiber and carboxymethyl cellulose into 30% ethanol solution, keep warm and activate for 1.5 hours, and keep warm at 40°C;
[0046] (3) Mix silk fiber, coconut fiber, xanthan gum, sorbitol and sodium alginate into 5% boric acid solution, use ultrasonic pulverizer, ultrasonic pulverize for 80 minutes, the power of ultrasonic pulverizer is 200W;
[0047] (4) Mix the sol...
PUM
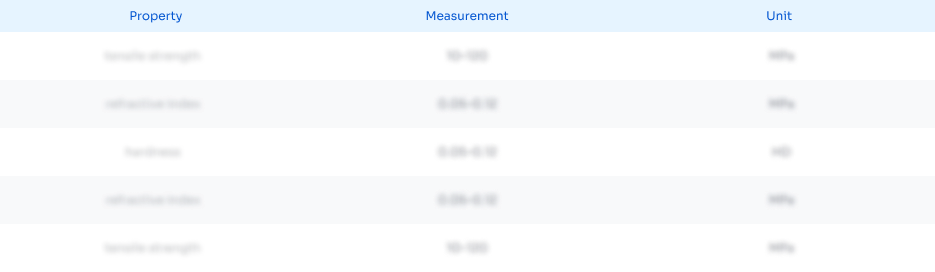
Abstract
Description
Claims
Application Information

- R&D
- Intellectual Property
- Life Sciences
- Materials
- Tech Scout
- Unparalleled Data Quality
- Higher Quality Content
- 60% Fewer Hallucinations
Browse by: Latest US Patents, China's latest patents, Technical Efficacy Thesaurus, Application Domain, Technology Topic, Popular Technical Reports.
© 2025 PatSnap. All rights reserved.Legal|Privacy policy|Modern Slavery Act Transparency Statement|Sitemap|About US| Contact US: help@patsnap.com