Composite coating material based on 45# steel substrate and preparing method of coating
A 45# steel, composite coating technology, applied in the direction of metal material coating process, coating, etc., can solve problems such as cracking, achieve the effect of not easy to crack, simple preparation process, and improve wear resistance and corrosion resistance
- Summary
- Abstract
- Description
- Claims
- Application Information
AI Technical Summary
Problems solved by technology
Method used
Image
Examples
Embodiment 1
[0039] Coating material formula: WC powder: 5%, Y 2 o 3 Powder: 5%, the balance is 304 stainless steel powder.
[0040] The production method of the coating material: add the 304 stainless steel ball milling medium with a ball-to-material ratio of 10:1 and the powder described in the formula into a 304 stainless steel ball mill pot, perform ball milling for 5 hours, and the ball milling speed is 150r / min to obtain laser cladding powder; The laser cladding powder was vacuum-dried at 120°C for 1 hour to obtain the coating material.
Embodiment 2
[0042] Coating material formula: WC powder: 0.1%, Y 2 o 3 Powder: 1%, the balance is 304 stainless steel powder.
[0043] Coating material production method: add 304 stainless steel ball milling medium with a ball-to-material ratio of 10:1 and the powder described in the formula into a 304 stainless steel ball mill pot, and perform ball milling for 4 hours at a milling speed of 180r / min to obtain laser cladding powder; The cladding powder was vacuum-dried at 100°C for 1.5 hours to obtain the coating material.
Embodiment 3
[0045] Coating material formula: WC powder: 10%, Y 2 o 3 Powder: 0.1%, the balance is 304 stainless steel powder.
[0046] Coating material production method: put the agate ball milling medium with a ball-to-material ratio of 10:1 and the powder described in the formula into the agate ball mill pot, and perform ball milling for 4 hours at a milling speed of 120r / min to obtain laser cladding powder; then laser cladding The powder was vacuum-dried at 150° C. for 0.8 h to obtain a coating material.
PUM
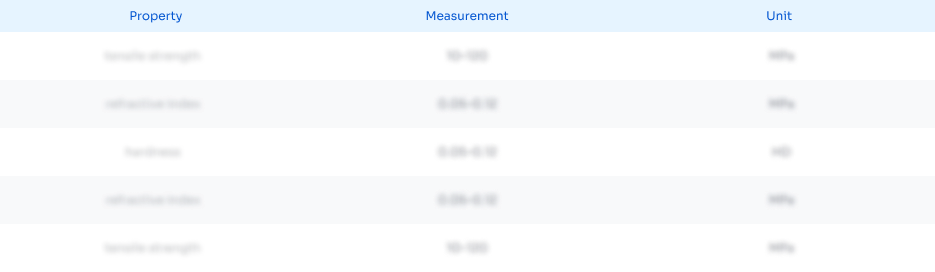
Abstract
Description
Claims
Application Information

- Generate Ideas
- Intellectual Property
- Life Sciences
- Materials
- Tech Scout
- Unparalleled Data Quality
- Higher Quality Content
- 60% Fewer Hallucinations
Browse by: Latest US Patents, China's latest patents, Technical Efficacy Thesaurus, Application Domain, Technology Topic, Popular Technical Reports.
© 2025 PatSnap. All rights reserved.Legal|Privacy policy|Modern Slavery Act Transparency Statement|Sitemap|About US| Contact US: help@patsnap.com