Preparation method for coating on electrolytic aluminum prebaked anode steel claw
A technology of prebaking anodes and anode steel claws, which is applied in the field of metallurgical materials, can solve the problems of electrolyte cryolite corrosion, high-temperature oxidation consumption of anode steel claws, etc., and achieve the effects of reducing consumption, improving comprehensive mechanical properties, and requiring less equipment
- Summary
- Abstract
- Description
- Claims
- Application Information
AI Technical Summary
Problems solved by technology
Method used
Image
Examples
Embodiment approach 1
[0024] Implementation mode one: if figure 1 As shown, the preparation method of the electrolytic aluminum prebaked anode steel claw coating of the present embodiment is:
[0025] (1) Grinding to remove the dirt on the surface of the anode steel claw, cleaning with 5wt% hydrochloric acid, absolute ethanol and deionized water, then drying at 20°C, and then using degreasing agent to remove oil in turn (The degreasing agent is made of the KOH of 25wt% by mass percentage, the Na of 5wt% 2 SO 4 and 15wt% Na 2 CO 3 The mixed aqueous solution prepared by adding water, the degreasing process is to keep the degreasing agent boiling for 25 minutes), acid derusting (using sulfuric acid, the concentration of sulfuric acid derusting is 20wt%, the temperature is 60 ℃, and the heating time is 12 minutes);
[0026] (2) Hot-dip aluminizing the pretreated anode steel claws: put the pretreated anode steel claws in ZnCl 2 In the solution, the pretreated anode steel claws are treated with ZnCl...
Embodiment approach 2
[0028] Implementation mode two: if figure 1 As shown, the preparation method of the electrolytic aluminum prebaked anode steel claw coating of the present embodiment is:
[0029] (1) Grinding to remove the dirt on the surface of the anode steel claw, cleaning with 5wt% hydrochloric acid, absolute ethanol and deionized water, then drying at 50°C, and then degreasing with degreasing agent in turn (The degreasing agent is made of the KOH of 15wt% by mass percentage, the Na of 10wt% 2 SO 4 and 11wt% Na 2 CO 3The mixed aqueous solution prepared by adding water, the degreasing process is to keep the degreasing agent boiling for 20 minutes), acid derusting (using sulfuric acid, the concentration used for sulfuric acid derusting is 30wt%, the temperature is 40°C, and the heating time is 15 minutes);
[0030] (2) Hot-dip aluminizing the pretreated anode steel claws: put the pretreated anode steel claws in ZnCl 2 In the solution, the pretreated anode steel claws were placed in ZnCl...
Embodiment approach 3
[0032] Implementation mode three: if figure 1 As shown, the preparation method of the electrolytic aluminum prebaked anode steel claw coating of the present embodiment is:
[0033] (1) Grinding to remove the dirt on the surface of the anode steel claw, cleaning with hydrochloric acid with a concentration of 5wt%, absolute ethanol and deionized water, then drying at 70°C, and then degreasing with degreasing agent in turn (The degreasing agent is made of the KOH of mass percentage 22wt%, the Na of 8wt% 2 SO 4 and 5wt% Na 2 CO 3 The mixed aqueous solution prepared by adding water, the degreasing process is to keep the degreasing agent boiling for 30 minutes), acid derusting (using sulfuric acid, the concentration used for sulfuric acid derusting is 22wt%, the temperature is 50 ℃, and the heating time is 10 minutes);
[0034] (2) Hot-dip aluminizing the pretreated anode steel claws: put the pretreated anode steel claws in ZnCl 2 In the solution, the pretreated anode steel cla...
PUM
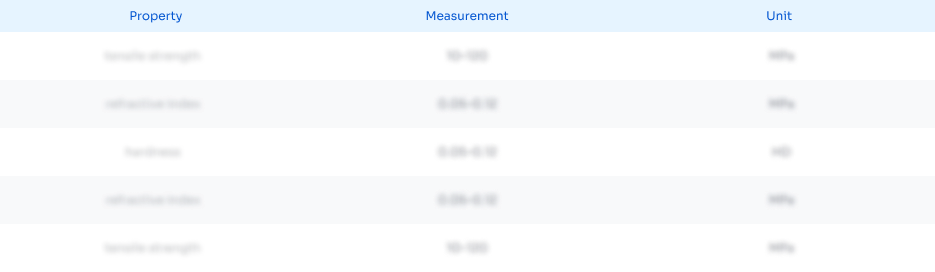
Abstract
Description
Claims
Application Information

- Generate Ideas
- Intellectual Property
- Life Sciences
- Materials
- Tech Scout
- Unparalleled Data Quality
- Higher Quality Content
- 60% Fewer Hallucinations
Browse by: Latest US Patents, China's latest patents, Technical Efficacy Thesaurus, Application Domain, Technology Topic, Popular Technical Reports.
© 2025 PatSnap. All rights reserved.Legal|Privacy policy|Modern Slavery Act Transparency Statement|Sitemap|About US| Contact US: help@patsnap.com