Production method of extra-thick high-purify plastic mold steel plate
A plastic mold and production method technology, applied in the field of metallurgy, can solve problems such as insufficient penetration and deformation of blanks, unguaranteed quality of steel plates, and insufficient compression ratio, etc., to achieve easy operation and reduce the process of forging blanks for electroslag remelting round ingots , smooth surface effect
- Summary
- Abstract
- Description
- Claims
- Application Information
AI Technical Summary
Problems solved by technology
Method used
Examples
Embodiment 1
[0026] The steel type in this example is WSM718R, the thickness of the steel plate is 275mm, and the compression ratio is 3.49; the composition weight percentages are: C: 0.36%, Si: 0.27%, Mn: 1.20%, P: 0.018%, S: 0.010% , Ni: 1.00%, Cr: 2.00%, Mo: 0.50%, TAl0.027%, the balance is Fe and unavoidable impurities.
[0027] Process steps: (1) Smelting process: including electric furnace steelmaking, LF refining and vacuum treatment steps; the electric furnace steelmaking step adopts ultra-high power electric arc furnace, selects high-quality raw materials, and adopts large slag flow slag operation during the melting period to avoid slag tapping ; After tapping, the molten steel is sent to the LF refining furnace for LF refining, rapid deoxidation and desulphurization, and the reducing slag is removed after adjusting the temperature and composition; re-making the reducing slag in the VD / VOD furnace for vacuum degassing treatment The medium vacuum is 67Pa and the holding time is 20m...
Embodiment 2
[0039] The steel type WSM718R in this embodiment has a steel plate thickness of 185mm and a compression ratio of 4.10; the composition weight percentages are: C: 0.35%, Si: 0.20%, Mn: 1.10%, P: 0.018%, S: 0.008%, Ni: 1.25%, Cr: 1.90%, Mo: 0.40%, TAl0.022%, the balance is Fe and unavoidable impurities.
[0040] The processing steps of the production method of the extra thick high-purity plastic mold steel plate are as follows:
[0041](1) Smelting process: including electric furnace steelmaking, LF refining and vacuum treatment steps; the electric furnace steelmaking step uses an ultra-high-power electric arc furnace, selects high-quality raw materials, and adopts a large slag flow operation during the melting period to avoid slag and tap the steel; Finally, the molten steel is sent to the LF refining furnace for LF refining, rapid deoxidation and desulphurization, and the reducing slag is removed after adjusting the temperature and composition; the reducing slag is recreated i...
Embodiment 3
[0053] The steel type WSMP20R of this embodiment has a steel plate thickness of 420 mm and a compression ratio of 2.28; the composition weight percentages are: C: 0.40%, Si: 0.36%, Mn: 1.50%, P: 0.020%, S: 0.010%, Cr: 1.80%, Ni: 0.05%, Mo: 0.50%, TAl 0.050%, the balance is Fe and unavoidable impurities, and the balance is Fe and unavoidable impurities.
[0054] Except for the following differences, the rest of the process steps are the same as in Example 1: (1) Smelting process: the vacuum degree is 65 Pa, and the vacuum is broken when the vacuum holding time is 30 minutes.
[0055] (3) Electroslag remelting process: Add Al particles at 30g / min; select a 700mm water-cooled crystallizer for remelting, and control the average melting rate at 20kg / min.
[0056] (5) Heating process: put the electroslag ingot into the furnace to simmer steel for 60 minutes, then use low-speed steel burning, the heating rate below 1000 ℃ is 120 ℃ / h, the maximum heating temperature is 1230 ℃, and the...
PUM
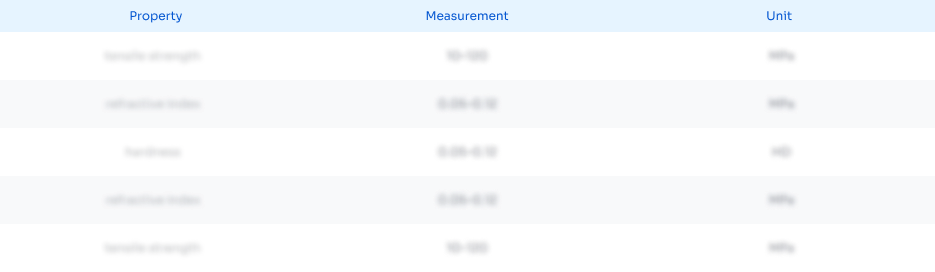
Abstract
Description
Claims
Application Information

- Generate Ideas
- Intellectual Property
- Life Sciences
- Materials
- Tech Scout
- Unparalleled Data Quality
- Higher Quality Content
- 60% Fewer Hallucinations
Browse by: Latest US Patents, China's latest patents, Technical Efficacy Thesaurus, Application Domain, Technology Topic, Popular Technical Reports.
© 2025 PatSnap. All rights reserved.Legal|Privacy policy|Modern Slavery Act Transparency Statement|Sitemap|About US| Contact US: help@patsnap.com