Desulphurization and denitrogenation integrated method
A desulfurization, denitrification and denitrification technology, which is applied in chemical instruments and methods, separation methods, gas treatment, etc., can solve the problems of incomplete desulfurization and denitrification, low utilization rate, and low reaction rate, so as to reduce the cost of desulfurization and denitrification, and reduce air pollution substances, and the effect of avoiding waste water pollution
- Summary
- Abstract
- Description
- Claims
- Application Information
AI Technical Summary
Problems solved by technology
Method used
Image
Examples
Embodiment 1
[0062] a kind of like figure 1 The integrated desulfurization and denitrification method of the present invention comprises the following steps:
[0063] (1) Two parts of pyrolusite and brown manganese ore containing Mn21.6% and electrolytic MnO 2 Add the mixture of two fixed-bed reactors in series into reactor A and reactor B formed by two fixed-bed reactors in series;
[0064] (2) Heat reactor A to 150°C; heat reactor B to 100°C;
[0065] (3) Will contain SO2 1500ppm, NO x 500ppm mixed gas of non-ferrous smelter waste gas, thermal power plant waste gas and boiler waste gas is passed into reactor A, and desulfurization reaction is carried out at 150°C to obtain desulfurized tail gas I and desulfurized manganese ore;
[0066] (4) Combine the desulfurization tail gas I of the above step (3) with a certain amount of NH 3 mixed (where NH 3 / NO x =2.4), then pass it into reactor B, and carry out denitrification reaction at 100°C to obtain desulfurization and denitrification ...
Embodiment 2
[0070] a kind of like figure 1 The integrated desulfurization and denitrification method of the present invention comprises the following steps:
[0071] (1) Add two mixtures of metamanganate, manganite and manganite containing Mn34.3% into moving bed reactor A and moving bed reactor B respectively;
[0072] (2) Heat reactor A to 350°C; heat reactor B to 350°C;
[0073] (3) Will contain SO 2 2800ppm, NO x 150ppm non-ferrous smelter waste gas is passed into reactor A, and desulfurization reaction is carried out at 350°C to obtain desulfurized tail gas I and desulfurized manganese ore;
[0074] (4) Combine the desulfurization tail gas I of the above step (3) with a certain amount of NH 3 mixed (where NH 3 / NO x =0.7), then pass it into reactor B, and carry out denitrification reaction at 350°C to obtain desulfurization and denitrification tail gas II and denitrification manganese ore; through detection and calculation, the desulfurization rate is greater than 99.5%, the de...
Embodiment 3
[0078] a kind of like figure 1 The integrated desulfurization and denitrification method of the present invention comprises the following steps:
[0079] (1) Add two mixtures of pyrolusite and hydromanganese containing Mn19.51% into fluidized bed reactor A and fluidized bed reactor B respectively;
[0080] (2) Heat reactor A to 450°C; heat reactor B to 200°C;
[0081] (3) Will contain SO 2 2500ppm, NO x The mixed gas of 1000ppm non-ferrous smelter exhaust gas and boiler exhaust gas is fed into reactor A, and desulfurization reaction is carried out at 450°C to obtain desulfurization tail gas I and desulfurization manganese ore. The desulfurization curve is shown in the attached figure 2 As shown, the measured SO in the desulfurization tail gas 2 <5ppm, the desulfurization rate is over 99.8%;
[0082] (4) Combine the desulfurization tail gas I of the above step (3) with a certain amount of NH 3 mixed (where NH 3 / NO x =1.2), and then pass it into reactor B, and carry ou...
PUM
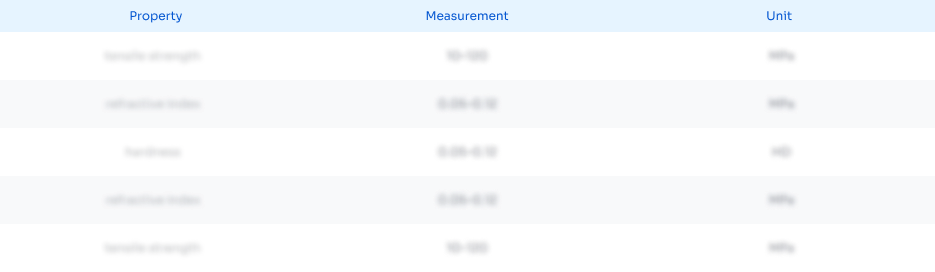
Abstract
Description
Claims
Application Information

- R&D Engineer
- R&D Manager
- IP Professional
- Industry Leading Data Capabilities
- Powerful AI technology
- Patent DNA Extraction
Browse by: Latest US Patents, China's latest patents, Technical Efficacy Thesaurus, Application Domain, Technology Topic, Popular Technical Reports.
© 2024 PatSnap. All rights reserved.Legal|Privacy policy|Modern Slavery Act Transparency Statement|Sitemap|About US| Contact US: help@patsnap.com