Method for controlling blank casting quality of phi-280mm 37Mn circular tube blank
A quality control method and round tube billet technology, applied in the field of iron and steel metallurgy, can solve the problems of large radial temperature gradient, large linear expansion coefficient, slow solidification and cooling, etc., and achieve the improvement of porosity rating, crack defect control, liquid steel composition and the effect of temperature homogenization
- Summary
- Abstract
- Description
- Claims
- Application Information
AI Technical Summary
Problems solved by technology
Method used
Examples
Embodiment
[0025] A steelmaking plant uses 120t converter smelting → LF furnace refining → RH vacuum treatment → six-machine six-strand casting machine φ280mm section continuous casting to produce 37Mn round pipe billets. At the end of converter blowing, the end point carbon is controlled at 0.10%, and the end point temperature is controlled at 1673℃; after the tapping is completed, the thickness of the slag layer is 72mm; the small platform presses at 1.7m / t steel Feed the aluminum wire for deoxidation; the mass percentage control of the outbound components of the small platform is: [C] 0.32%, [Si] 0.21%, [Mn] 1.20%, [P] 0.011%; after deoxidation and alloying, soft argon blowing and stirring , The stirring time is 6.5min, and the molten steel is not exposed during stirring.
[0026] The molten steel arrives at the LF refining furnace, and the molten steel is blown with argon. The molten steel fluctuates slightly without major turning. After the refining, Ti is added at 0.020% of the weight...
PUM
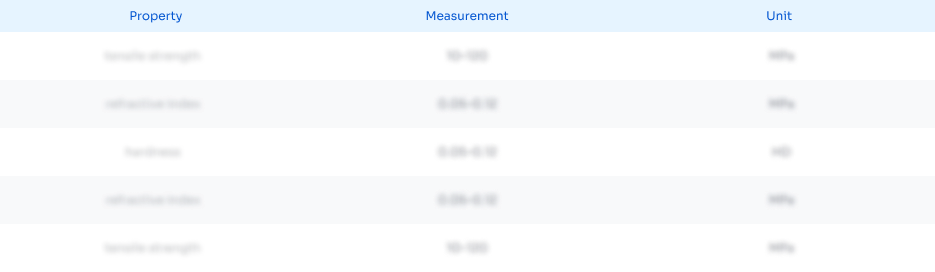
Abstract
Description
Claims
Application Information

- Generate Ideas
- Intellectual Property
- Life Sciences
- Materials
- Tech Scout
- Unparalleled Data Quality
- Higher Quality Content
- 60% Fewer Hallucinations
Browse by: Latest US Patents, China's latest patents, Technical Efficacy Thesaurus, Application Domain, Technology Topic, Popular Technical Reports.
© 2025 PatSnap. All rights reserved.Legal|Privacy policy|Modern Slavery Act Transparency Statement|Sitemap|About US| Contact US: help@patsnap.com