Environment-friendly soundproof material and preparation method thereof
A sound insulation material and technology for environmental protection, applied in the field of environmental protection sound insulation materials and their preparation, can solve the problems of poor sound insulation effect, high energy consumption of materials, environmental pollution, etc., and achieve the effects of stable performance, good mechanical strength and simple preparation method.
- Summary
- Abstract
- Description
- Claims
- Application Information
AI Technical Summary
Problems solved by technology
Method used
Image
Examples
Embodiment 1
[0025] (1) Weigh 60 kg of polyethylene, 18 kg of propenyl phenyl isopentenyl ether, 3 kg of polyoxyethylene stearate, 3 kg of polyglycerin fatty acid ester, 2 kg of sodium silicate, 1 kg of sodium bicarbonate, bis(2-chloro Ethyl) dichlorophosphoramide 1kg, hexadecyl mercaptan 1kg and dipentyl succinate sodium sulfonate 0.2kg, mix them evenly, add them to the reactor and stir at 110°C for 1 hour;
[0026] (2) Add to the twin-screw extruder, add 20kg of hemp fiber, 10kg of calcium carbonate, and 5kg of starch phosphate monoester to the side feeding port of the twin-screw extruder, melt, extrude, dry, and pellet to obtain environmentally friendly sound insulation materials .
[0027] The temperature of each section of the twin-screw extruder is 170°C in the first zone, 190°C in the second zone, 220°C in the third zone, and 200°C in the fourth zone.
[0028] Table 1 shows the performance test results of the environmentally friendly sound insulation materials.
Embodiment 2
[0030] (1) Weigh 60 kg of polyethylene, 18 kg of propenyl phenyl isopentenyl ether, 3 kg of polyoxyethylene stearate, 3 kg of polyglycerin fatty acid ester, 2 kg of sodium silicate, 1 kg of sodium bicarbonate, bis(2-chloro Ethyl) dichlorophosphoramide 1kg, hexadecanethiol 1kg, dipentyl succinate sodium sulfonate 0.2kg and polyvinyl butyral 1kg, mix well, add to the reactor, stir at 110°C hour;
[0031] (2) Add to the twin-screw extruder, add 20kg of hemp fiber, 10kg of calcium carbonate, and 5kg of starch phosphate monoester to the side feeding port of the twin-screw extruder, melt, extrude, dry, and pellet to obtain environmentally friendly sound insulation materials .
[0032] The temperature of each section of the twin-screw extruder is 170°C in the first zone, 190°C in the second zone, 220°C in the third zone, and 200°C in the fourth zone.
[0033] Table 1 shows the performance test results of the environmentally friendly sound insulation materials.
Embodiment 3
[0035] (1) Weigh 70 kg of polyethylene, 25 kg of propenyl phenyl isopentenyl ether, 6 kg of polyoxyethylene stearate, 5 kg of polyglycerin fatty acid ester, 5 kg of sodium silicate, 3 kg of sodium bicarbonate, bis(2-chloro Ethyl) dichlorophosphoramide 2kg, n-hexadecanethiol 2kg, dipentyl succinate sodium sulfonate 0.8kg and polyvinyl butyral 1kg, mix well, add to the reactor, stir at 120°C for 2 hour;
[0036] (2) Put into the twin-screw extruder, add 25kg of bamboo fiber, 15kg of calcium carbonate, 8kg of starch phosphate monoester to the side feed port of the twin-screw extruder, melt, extrude, dry, and pellet to obtain environmentally friendly sound insulation materials .
[0037] The temperature of each zone of the twin-screw extruder is 180°C in the first zone, 210°C in the second zone, 230°C in the third zone, and 210°C in the fourth zone.
[0038] Table 1 shows the performance test results of the environmentally friendly sound insulation materials.
PUM
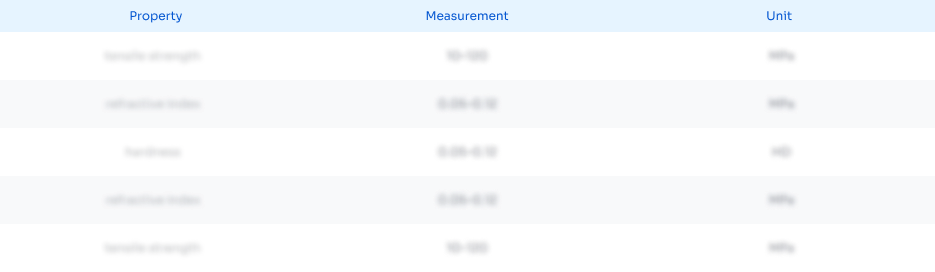
Abstract
Description
Claims
Application Information

- R&D
- Intellectual Property
- Life Sciences
- Materials
- Tech Scout
- Unparalleled Data Quality
- Higher Quality Content
- 60% Fewer Hallucinations
Browse by: Latest US Patents, China's latest patents, Technical Efficacy Thesaurus, Application Domain, Technology Topic, Popular Technical Reports.
© 2025 PatSnap. All rights reserved.Legal|Privacy policy|Modern Slavery Act Transparency Statement|Sitemap|About US| Contact US: help@patsnap.com