Rubber asphalt composite material with excellent cold resistance
A composite material and rubber asphalt technology, applied in asphalt coatings, coatings and other directions, can solve the problems of water seepage of the coated object, affecting the use, and increasing the cost, and achieve the effect of controllable cost and convenient production.
- Summary
- Abstract
- Description
- Claims
- Application Information
AI Technical Summary
Problems solved by technology
Method used
Examples
Embodiment 1
[0054] Rubber asphalt composite material with excellent cold resistance, composed of the following components:
[0055] 75 parts of anionic emulsified asphalt; 25 parts of anionic neoprene latex; 7 parts of DBTP; 0.5 parts of defoamer, 0.5 parts of pine tar soap, 1.0 parts of sodium naphthalenesulfonic acid condensate, 1.5 parts of sodium alkyl sulfate, hydrophilicity 2 -1.0 part of (2-hydroxyphenyl)-benzotriazole ultraviolet absorber; the pH value of the system is 9-13.
[0056] Anionic emulsified bitumen is commercially available.
[0057]Mix the components in proportion at room temperature to obtain a rubber asphalt composite material with excellent cold resistance.
[0058] Cold resistance test:
[0059] The resulting composite material is placed in a spray gun as component A;
[0060] The curing agent (calcium chloride or sodium chloride, the concentration is 10-20wt%) is placed in another spray gun as component B;
[0061] Turn on the spray gun, mix and spray the two...
Embodiment 2
[0064] Rubber asphalt composite material with excellent cold resistance, composed of the following components:
[0065] 65 parts of anionic emulsified asphalt; 15 parts of anionic styrene-butadiene rubber latex; 20 parts of anionic nitrile rubber latex; 5 parts of DBP; 1.0 parts of defoamer, 2.5 parts of fatty acid soap, 0.5 parts of p-nonylphenyl polyethoxylate, 0.5 part of sodium dibutylphenylphenol disulfonate, 0.5 part of hindered amine light stabilizer; the pH value of the system is 9-13.
[0066] Mix the components in proportion at room temperature to obtain a rubber asphalt composite material with excellent cold resistance.
[0067] The cold resistance test method is the same as that of Example 1, and the result: the waterproof coating film using the composite material of Example 2 still has no brittle failure at -40°C.
Embodiment 3
[0069] Rubber asphalt composite material with excellent cold resistance, composed of the following components:
[0070] 78 parts of anionic emulsified asphalt; 12 parts of anionic EPDM rubber latex; 10 parts of anionic polyisoprene rubber latex; 4 parts of DOA; 1.0 parts of defoamer, 2.5 parts of alkyl diphenyl ether disulfonate, alkyl 0.5 part of sodium aryl sulfonate, 0.5 part of olein sulfonate sodium salt, and 0.5 part of Hals; the pH value of the system is 9-13.
[0071] Mix the components in proportion at room temperature to obtain a rubber asphalt composite material with excellent cold resistance.
[0072] The cold resistance test method is the same as that of Example 1, and the result: the waterproof coating film using the composite material of Example 3 still does not undergo brittle failure at -40°C.
PUM
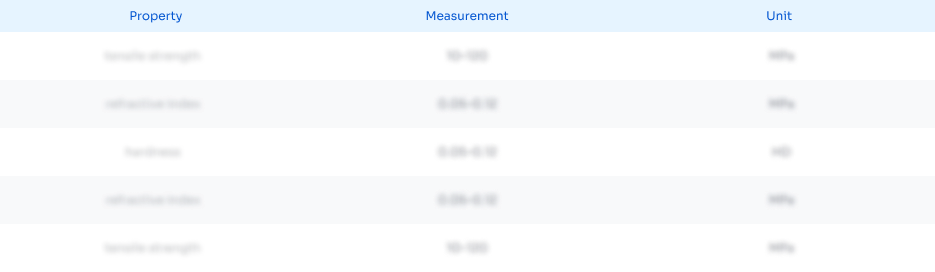
Abstract
Description
Claims
Application Information

- Generate Ideas
- Intellectual Property
- Life Sciences
- Materials
- Tech Scout
- Unparalleled Data Quality
- Higher Quality Content
- 60% Fewer Hallucinations
Browse by: Latest US Patents, China's latest patents, Technical Efficacy Thesaurus, Application Domain, Technology Topic, Popular Technical Reports.
© 2025 PatSnap. All rights reserved.Legal|Privacy policy|Modern Slavery Act Transparency Statement|Sitemap|About US| Contact US: help@patsnap.com