Downlink high-temperature gasified product chilling device
A technology of chilling and product, applied in the field of descending high-temperature gasification product chilling device, can solve problems such as volume ratio difference, and achieve the effects of increasing volume concentration, increasing radiative heat transfer coefficient, and reducing the design of heating surface
- Summary
- Abstract
- Description
- Claims
- Application Information
AI Technical Summary
Problems solved by technology
Method used
Image
Examples
Embodiment 1
[0042] figure 1 Schematic diagram of the structure of the downward-type high-temperature gasification product quenching device provided for this embodiment. The downward-type high-temperature gasification product quenching device includes three main components, namely the gasification section, the quenching section, and the cooler section. .
[0043] The gasifier adopts the design of gas slag flowing downward, the gasifier adopts the water wall design, the tapered slag mouth at the bottom and the straight section of the slag mouth adopt coil type water cooling wall, and there is a ring-shaped chilling channel under the straight section of the slag mouth, and the chilling The front section of the channel is connected by a coil-type water-cooled wall, and the chilled gas header is used to distribute the synthesis gas, and the chilled gas is connected through the chilled gas inlet pipe. A syngas cooler is provided below the chilling channel. The body of the gasifier, the quench...
Embodiment 2
[0078] figure 2 The structure schematic diagram of the down-type high-temperature gasification product quenching device provided for this embodiment, the down-type high-temperature gasification product quenching device is basically the same as that of Example 1, the main difference is: the cylinder of the syngas cooler 3 The upper part of the water wall 7 is directly connected to the chilling channel 4, so the front section of the chilling channel 4 is directly connected to the cylinder water wall 7 of the syngas cooler 3, without the need for a coiled water wall 13; however, the chilling channel 4. The water-cooled wall coil 11 on the inner wall of the lower slag port 2 in the front section and the straight section is still connected by a coil-type water-cooled wall 13.
PUM
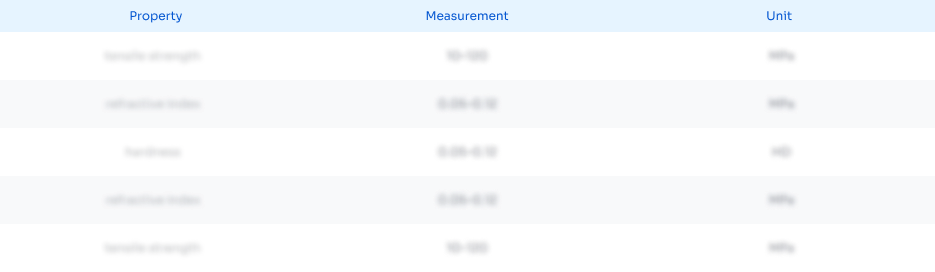
Abstract
Description
Claims
Application Information

- Generate Ideas
- Intellectual Property
- Life Sciences
- Materials
- Tech Scout
- Unparalleled Data Quality
- Higher Quality Content
- 60% Fewer Hallucinations
Browse by: Latest US Patents, China's latest patents, Technical Efficacy Thesaurus, Application Domain, Technology Topic, Popular Technical Reports.
© 2025 PatSnap. All rights reserved.Legal|Privacy policy|Modern Slavery Act Transparency Statement|Sitemap|About US| Contact US: help@patsnap.com