Method for preparing g-C3N4 hollow fiber film on large scale
A g-c3n4, fiber membrane technology, applied in chemical instruments and methods, membrane technology, semi-permeable membrane separation, etc., can solve problems such as difficulty in large-scale production, simplification, miniaturization, and intensification of membrane components.
- Summary
- Abstract
- Description
- Claims
- Application Information
AI Technical Summary
Problems solved by technology
Method used
Image
Examples
Embodiment
[0020] The first step: Weigh 10g of melamine and put it into a crucible, put the crucible into a muffle furnace, burn it in the air at a temperature of 500°C for 3 hours, and cool it down to room temperature naturally to obtain g-C 3 N 4 Block;
[0021] Step 2: Take out 5g of g-C 3 N 4 block, uniformly ground to obtain g-C 3 N 4 Powder;
[0022] Step 3: Add 5g of g-C 3 N 4 Put the powder into a muffle furnace, burn it in the air at a temperature of 550°C for 2 hours, and cool it down to room temperature naturally to obtain g-C 3 N 4 Nanosheets;
[0023] Step 4: Weigh 1g of g-C 3 N 4 Nanosheets were dispersed in 10 mL of N,N-dimethylformamide, and stirred continuously for 3 hours until uniformly dispersed, then 0.5 g of polyvinyl butyral was added to the dispersed solution, and continuously stirred on a strong stirrer Stir for 6 hours until uniformly dispersed to obtain g-C 3 N 4 Casting solution;
[0024] Step 5: Pass the casting solution at 25mL / h and water at ...
PUM
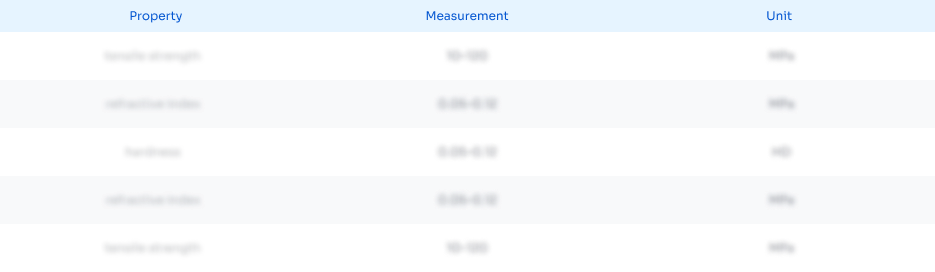
Abstract
Description
Claims
Application Information

- R&D Engineer
- R&D Manager
- IP Professional
- Industry Leading Data Capabilities
- Powerful AI technology
- Patent DNA Extraction
Browse by: Latest US Patents, China's latest patents, Technical Efficacy Thesaurus, Application Domain, Technology Topic, Popular Technical Reports.
© 2024 PatSnap. All rights reserved.Legal|Privacy policy|Modern Slavery Act Transparency Statement|Sitemap|About US| Contact US: help@patsnap.com