Mullite ceramic hollow fiber membrane and preparation method for same
A technology of fiber membrane and mullite, which is applied in the field of mullite ceramic hollow fiber membrane and its preparation, can solve the problems of high cost of ceramic membrane preparation, high sintering temperature, poor mechanical strength, etc., and achieve whisker aspect ratio can be achieved control, low sintering temperature, and achieve the effect of reduction
- Summary
- Abstract
- Description
- Claims
- Application Information
AI Technical Summary
Problems solved by technology
Method used
Image
Examples
Embodiment 1
[0027] Example 1: Preparation of Mullite Ceramic Hollow Fiber Membrane
[0028] According to the following steps: preparing polymer solution, preparing ceramic-polymer slurry, spinning membrane green body and sintering treatment, preparing low-cost reinforced mullite ceramic hollow fiber membrane, wherein:
[0029] 1 Preparation of polymer solution:
[0030] This example organic polymer is polyether sulfone (PES); Solvent is N-methylpyrrolidone; Additive is polyvinylpyrrolidone (PVP); The weight composition of each component when preparing polymer solution is: organic polymer: solvent: additive =18g:72g:2g; first dissolve the proportioned organic polymer and additives in the organic solvent, and wet ball milling and mixing for 24 hours to completely dissolve it to make a polymer solution;
[0031] 2 Preparation of ceramic-polymer slurry:
[0032] Add ceramic powder with a particle size distribution of 0.05-10 μm and an average particle size of 1.8 μm to the above polymer sol...
PUM
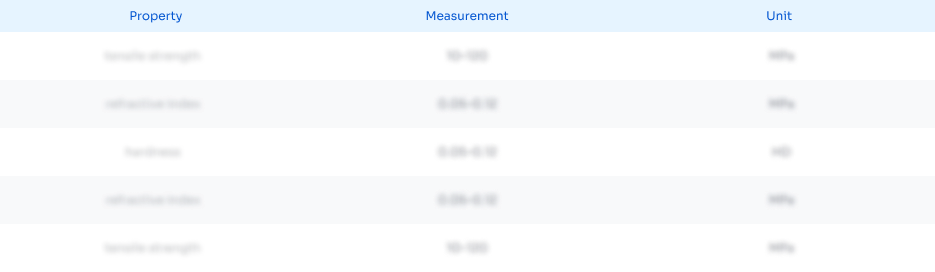
Abstract
Description
Claims
Application Information

- R&D
- Intellectual Property
- Life Sciences
- Materials
- Tech Scout
- Unparalleled Data Quality
- Higher Quality Content
- 60% Fewer Hallucinations
Browse by: Latest US Patents, China's latest patents, Technical Efficacy Thesaurus, Application Domain, Technology Topic, Popular Technical Reports.
© 2025 PatSnap. All rights reserved.Legal|Privacy policy|Modern Slavery Act Transparency Statement|Sitemap|About US| Contact US: help@patsnap.com