Method for preparing cyclopentanol from cyclopentene
A technology for cyclopentene and cyclopentanol, applied in the field of preparing cyclopentanol from cyclopentene, can solve the problems of reduced reaction rate, extremely high requirements on equipment corrosion resistance, difficult recovery of concentrated sulfuric acid, etc., and achieves the effect of improving conversion rate
- Summary
- Abstract
- Description
- Claims
- Application Information
AI Technical Summary
Problems solved by technology
Method used
Image
Examples
Embodiment 1~10
[0033] 1. Esterification reaction
[0034] The esterification reaction is carried out in a tubular fixed-bed reactor with a size of φ25mm×1500mm. In the reactor, 50 grams of spherical sulfonic acid-based cation-exchange resin catalysts with an exchange portion of 0.40 to 1.25 mm in diameter are loaded into the reactor to form a fixed-bed catalyst bed. The mass exchange capacity of the resin is 5.0 mmol / g, and the exchange capacity of cerium ions is 10-30% of resin mass exchange capacity. The outside of the reactor is equipped with a temperature-controlled jacket of circulating hot water, and platinum resistors for temperature measurement are respectively installed on the upper, middle and lower parts of the catalyst bed. The amount of reaction feed is controlled by a feed pump, and the system pressure is regulated by a back pressure valve.
[0035]The reaction raw materials cyclopentene and acetic acid are reacted through the fixed bed according to the set feed amount, and t...
PUM
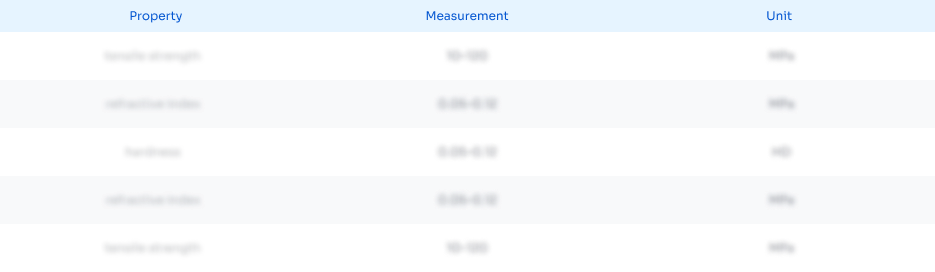
Abstract
Description
Claims
Application Information

- R&D Engineer
- R&D Manager
- IP Professional
- Industry Leading Data Capabilities
- Powerful AI technology
- Patent DNA Extraction
Browse by: Latest US Patents, China's latest patents, Technical Efficacy Thesaurus, Application Domain, Technology Topic, Popular Technical Reports.
© 2024 PatSnap. All rights reserved.Legal|Privacy policy|Modern Slavery Act Transparency Statement|Sitemap|About US| Contact US: help@patsnap.com