High temperature resistant and wear resistant rubber material for oil sealing
A rubber material, high temperature resistance technology, applied in the field of rubber, to achieve the effect of increasing wear resistance and mechanical properties, increasing mechanical properties, and excellent heat resistance
- Summary
- Abstract
- Description
- Claims
- Application Information
AI Technical Summary
Problems solved by technology
Method used
Examples
Embodiment 1
[0021] A high-temperature-resistant and wear-resistant rubber material for oil seals. The raw materials include, by weight, 50 parts of hydrogenated nitrile rubber, 50 parts of fluororubber, 10 parts of polytetrafluoroethylene, 60 parts of composite filler, and 10 parts of microencapsulated red phosphorus. , 15 parts of zinc borate, 20 parts of ammonium polyphosphate, 25 parts of acetyl trioctyl citrate, 15 parts of acetyl tributyl citrate, 3 parts of benzoyl peroxide, 0.2 parts of dibutyltin dilaurate, accelerator D0. 5 parts, 0.1 parts of accelerator ZDC, 2 parts of Ca / Zn composite stabilizer, 1 part of dibutyltin dichloride, 2 parts of rare earth stabilizer, 0.2 parts of anti-aging agent MB, 4450.4 parts of anti-aging agent, montan wax 2 copies;
[0022] Among them, the raw materials of composite fillers include: fumed silica, modified molybdenum disulfide, modified graphite, and modified silicon carbide, among which, fumed silica, modified molybdenum disulfide, modified gr...
Embodiment 2
[0027] A high-temperature-resistant and wear-resistant rubber material for oil seals. The raw materials include, by weight, 70 parts of hydrogenated nitrile rubber, 30 parts of fluororubber, 20 parts of polytetrafluoroethylene, 40 parts of composite filler, and 20 parts of microencapsulated red phosphorus. , 5 parts of zinc borate, 30 parts of ammonium polyphosphate, 15 parts of acetyl trioctyl citrate, 25 parts of acetyl tributyl citrate, 1 part of benzoyl peroxide, 0.4 parts of dibutyltin dilaurate, accelerator D0. 3 parts, 0.2 parts of accelerator ZDC, 1 part of Ca / Zn composite stabilizer, 2 parts of dibutyltin dichloride, 1 part of rare earth stabilizer, 0.4 parts of anti-aging agent MB, 4450.2 parts of anti-aging agent, montan wax 4 parts;
[0028]Among them, the raw materials of composite fillers include: fumed silica, modified molybdenum disulfide, modified graphite, and modified silicon carbide, among which, fumed silica, modified molybdenum disulfide, modified graphit...
Embodiment 3
[0033] A high-temperature-resistant and wear-resistant rubber material for oil seals, the raw materials of which include by weight: 55 parts of hydrogenated nitrile rubber, 45 parts of fluororubber, 12 parts of polytetrafluoroethylene, 55 parts of composite filler, and 13 parts of microencapsulated red phosphorus , 12 parts of zinc borate, 23 parts of ammonium polyphosphate, 23 parts of acetyl trioctyl citrate, 18 parts of acetyl tributyl citrate, 2.5 parts of benzoyl peroxide, 0.25 parts of dibutyltin dilaurate, accelerator D0. 45 parts, 0.13 parts of accelerator ZDC, 1.8 parts of Ca / Zn composite stabilizer, 1.3 parts of dibutyl tin dichloride, 1.8 parts of rare earth stabilizer, 0.25 parts of anti-aging agent MB, 4450.35 parts of anti-aging agent, montan wax 2.5 copies;
[0034] Among them, the raw materials of composite fillers include: fumed silica, modified molybdenum disulfide, modified graphite, and modified silicon carbide, among which, fumed silica, modified molybdenu...
PUM
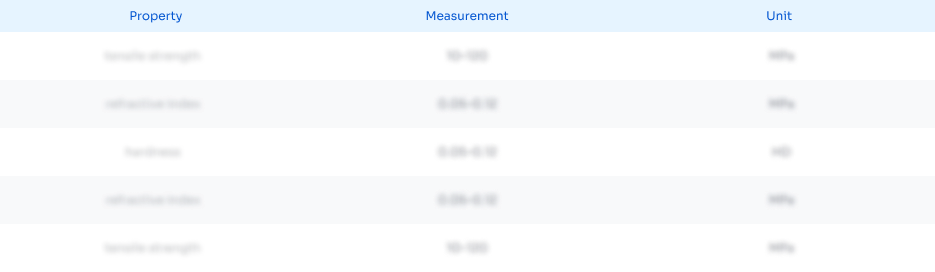
Abstract
Description
Claims
Application Information

- Generate Ideas
- Intellectual Property
- Life Sciences
- Materials
- Tech Scout
- Unparalleled Data Quality
- Higher Quality Content
- 60% Fewer Hallucinations
Browse by: Latest US Patents, China's latest patents, Technical Efficacy Thesaurus, Application Domain, Technology Topic, Popular Technical Reports.
© 2025 PatSnap. All rights reserved.Legal|Privacy policy|Modern Slavery Act Transparency Statement|Sitemap|About US| Contact US: help@patsnap.com