Manufacturing method for environment-friendly energy-saving fireproof antimagnetic and antistatic floor
An anti-static floor, environmental protection and energy saving technology, applied in the direction of manufacturing tools, flat products, pretreatment of molding materials, etc., to achieve the effect of saving resources, low formaldehyde emission, and improving mechanical properties
- Summary
- Abstract
- Description
- Claims
- Application Information
AI Technical Summary
Problems solved by technology
Method used
Image
Examples
Embodiment 1
[0045] An environment-friendly, energy-saving, fire-resistant, anti-magnetic, and anti-static floor manufacturing method, which comprises preparing flame retardant, wood fiber, carbon fiber, adding urea-formaldehyde glue, waterproofing agent paraffin chemical additives, etc. High temperature and high pressure one-time forming environmental protection, energy saving, fire prevention, anti-magnetic radiation, anti-static density board is characterized in that it specifically includes the following steps:
[0046] The first step: preparation of flame retardant:
[0047] 1) After mixing boron compounds (borax, zinc borate) and amine compounds (ethanolamine, dimethyl ethanol), raise the temperature to 60-120°C, hold the temperature for 40-60 minutes, and cool down to below 30°C to produce A polymer;
[0048] 1. Add titanium sulfate or zinc oxide to the aqueous solution of phosphorus compounds (diammonium phosphate, phosphate ester) and raise the temperature to 100-120°C fo...
Embodiment 2
[0059] In the first step, the preparation of the flame retardant: the flame retardant of the present invention is a resin type flame retardant, with boron, phosphorus, ammonium, nitrogen, titanium, silicon, zinc, aldehyde compounds, phosphorus compounds It decomposes into pyrophosphoric acid, dehydrates and carbonizes cellulose and hemicellulose into non-activated carbon under the catalysis of titanium and zinc, greatly reduces the heat release rate and heat release of the plate, promotes the interruption of combustion reaction, and prevents the spread of combustion; phosphorus compounds in nitrogen, Under the action of titanium and zinc compounds, the flame retardant effect will be greatly improved;
[0060] Nitrogen compounds will improve the flame retardant effect of phosphorus compounds; when a fire occurs, the flame retardant will release ammonia to reduce the oxygen content in the combustion body, causing the combustion body to be interrupted due to the lack of oxidan...
Embodiment 3
[0069] Preparation of wood fiber in the second step: use waste wood from forest trees, scraps from furniture factories, wooden door factories, floor factories, wood processing factories, veneer factories, waste wood, branch wood, secondary small-diameter wood, Artificial high-yield forests and other woods are used as raw materials, and the required wood fibers are prepared by cutting, planing or chipping, sorting, washing, softening, and heat grinding.
PUM
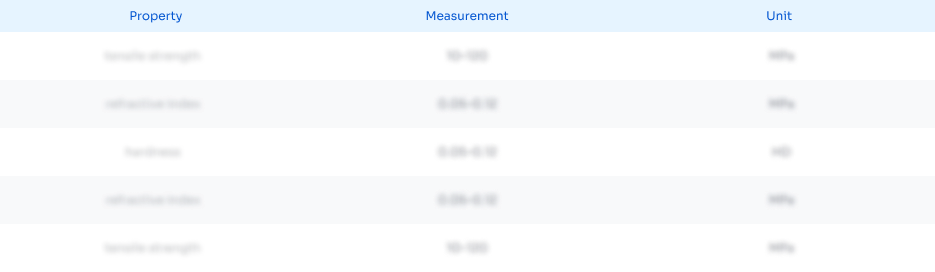
Abstract
Description
Claims
Application Information

- R&D Engineer
- R&D Manager
- IP Professional
- Industry Leading Data Capabilities
- Powerful AI technology
- Patent DNA Extraction
Browse by: Latest US Patents, China's latest patents, Technical Efficacy Thesaurus, Application Domain, Technology Topic.
© 2024 PatSnap. All rights reserved.Legal|Privacy policy|Modern Slavery Act Transparency Statement|Sitemap