Preparation method for powder-sintered porous metal body resistant to chlorine corrosion
A sintered metal and chlorine gas corrosion technology, which is applied in the field of powder sintered metal porous body preparation, can solve the problems of non-continuous production cost, long production cycle, complex process, etc., and achieve stable quality and pore structure, low production cost, The effect of simple preparation process
- Summary
- Abstract
- Description
- Claims
- Application Information
AI Technical Summary
Problems solved by technology
Method used
Image
Examples
Embodiment 1
[0024] Commercially used Ni powder, Cr powder and Fe powder with a particle size of 300 mesh were mixed according to the mass ratio of 75:18:7. The powder is mixed on a V-type mixer for 10 hours. After the mixed powder is granulated and dried with stearic acid, it is pressed with a pressure of 100MPa. green body. Then put the sample in a vacuum of 1×10 -3 Three-stage heat preservation and sintering in a vacuum furnace of Pa, the first stage: the sintering temperature is raised from room temperature to 400 °C, the heating rate is controlled at 5 °C / min, and the temperature is kept at 400 °C for 240 minutes; the second stage: the sintering temperature is raised to 750°C, the heating rate is controlled at 10°C / min, and held at 750°C for 180 minutes; the third stage: the sintering temperature is raised to 1200°C, the heating rate is controlled at 3°C / min, and held at 1200°C for 300 Minutes; after sintering, the product is obtained by cooling with the furnace.
[0025] The sint...
Embodiment 2
[0032] Mix commercial Ni powder with a particle size of 100 mesh, Cr powder and Fe powder with a particle size of 300 mesh at a mass ratio of 80:15:5. The powder is mixed on a V-type mixer for 10 hours. After the mixed powder is granulated and dried with stearic acid, it is pressed with a pressure of 250MPa. green body. Then put the sample in a vacuum of 1×10 -2 Three-stage heat preservation and sintering in a vacuum furnace of Pa, the first stage: the sintering temperature is raised from room temperature to 450 °C, the heating rate is controlled at 10 °C / min, and the temperature is kept at 450 °C for 120 minutes; the second stage: the sintering temperature is increased To 850°C, the heating rate was controlled at 5°C / min, and kept at 850°C for 90 minutes; the third stage: the sintering temperature was raised to 1350°C, the heating rate was controlled at 3°C / min, and kept at 1350°C for 180 Minutes; after sintering, the product is obtained by cooling with the furnace.
[00...
Embodiment 3
[0035] Commercially used Ni powder with a particle size of 300 mesh, Cr powder and Fe powder were mixed according to the mass ratio of 78:14:8. The powder is mixed on a V-type mixer for 10 hours. After the mixed powder is granulated and dried with stearic acid, it is pressed with a pressure of 150MPa. green body. Then put the sample in a vacuum of 5.6×10 -3 Three-stage heat preservation and sintering in a vacuum furnace of Pa, the first stage: the sintering temperature is raised from room temperature to 430 °C, the heating rate is controlled at 6 °C / min, and the temperature is kept at 430 °C for 180 minutes; the second stage: the sintering temperature is increased To 800°C, the heating rate is controlled at 6°C / min, and kept at 800°C for 120 minutes; the third stage: the sintering temperature is raised to 1300°C, the heating rate is controlled at 4°C / min, and kept at 1300°C for 240 Minutes; after sintering, the product is obtained by cooling with the furnace.
[0036]The s...
PUM
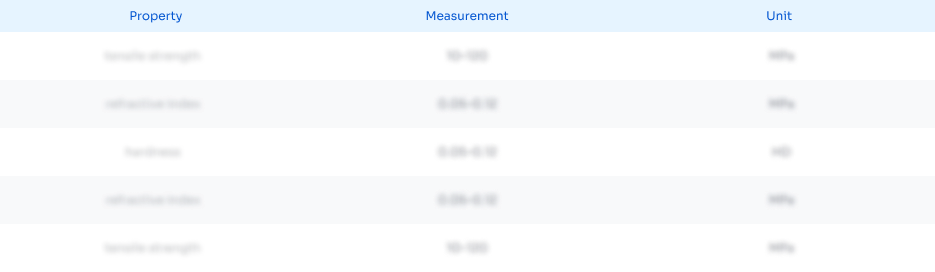
Abstract
Description
Claims
Application Information

- Generate Ideas
- Intellectual Property
- Life Sciences
- Materials
- Tech Scout
- Unparalleled Data Quality
- Higher Quality Content
- 60% Fewer Hallucinations
Browse by: Latest US Patents, China's latest patents, Technical Efficacy Thesaurus, Application Domain, Technology Topic, Popular Technical Reports.
© 2025 PatSnap. All rights reserved.Legal|Privacy policy|Modern Slavery Act Transparency Statement|Sitemap|About US| Contact US: help@patsnap.com