Flame brazing process method for stator coil bars and connector plates of power generator
A generator stator, flame brazing technology, applied in manufacturing tools, welding equipment, metal processing equipment and other directions, can solve the problems of low heating efficiency, poor joint brazing quality, poor temperature uniformity, etc., to improve labor productivity, reduce Labor cost, effect of improving heating efficiency and temperature uniformity
- Summary
- Abstract
- Description
- Claims
- Application Information
AI Technical Summary
Problems solved by technology
Method used
Image
Examples
Embodiment Construction
[0012] The present invention is a kind of flame brazing process method of generator stator wire bar and head plate, and specific embodiment is as follows: 1) carry out flame heating to the end of wire bar, wait for the organic matters such as insulating material between strands to melt and float to After the surface is finished, stop heating. After the wire rod is cooled, use an angle grinder to completely remove the oxides and pollutants on the surface of the wire rod end, and then scrub with absolute ethanol; 2) Sand the head plate brazing area and solder with sandpaper 3) Wrap the insulating part of the wire rod with water-soaked fireproof cloth to avoid burning the wire rod insulation during brazing; 4) The grade with a preset thickness of 0.2mm is BCu80AgP Copper-phosphorus brazing filler metal, such as figure 1 As shown, the first soldering piece 2 is placed between the upper layer wire bar end 3 and the left side tie plate 4, and the second welding piece 8 is placed bet...
PUM
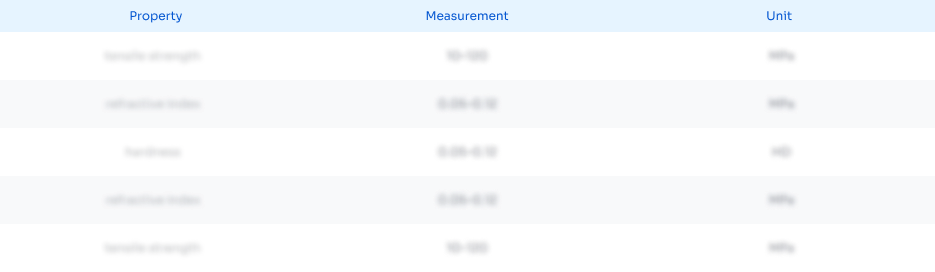
Abstract
Description
Claims
Application Information

- R&D Engineer
- R&D Manager
- IP Professional
- Industry Leading Data Capabilities
- Powerful AI technology
- Patent DNA Extraction
Browse by: Latest US Patents, China's latest patents, Technical Efficacy Thesaurus, Application Domain, Technology Topic, Popular Technical Reports.
© 2024 PatSnap. All rights reserved.Legal|Privacy policy|Modern Slavery Act Transparency Statement|Sitemap|About US| Contact US: help@patsnap.com