A kind of anti-ultraviolet finishing agent and preparation method thereof
An anti-ultraviolet and finishing agent technology, which is applied in fiber treatment, plant fiber, textiles and papermaking, etc., can solve the problems of mechanical and other performance degradation, affect the anti-ultraviolet effect, and poor particle compatibility, so as to prevent interface defects and avoid Easy to aggregate and improve performance
- Summary
- Abstract
- Description
- Claims
- Application Information
AI Technical Summary
Problems solved by technology
Method used
Image
Examples
preparation example Construction
[0011] Wherein, the preparation method of described nano titanium dioxide graft copolymer comprises the following steps
[0012] a. Weigh a certain amount of nano-titanium dioxide particles and silane coupling agent in absolute ethanol, stir evenly, disperse ultrasonically for 10 minutes, heat in a water bath to 50-70°C for 5 hours, dry at 80°C and grind to obtain modification Nano titanium dioxide particles;
[0013] b. Add the modified nano-titanium dioxide particles to a certain concentration of polymerizable emulsifier aqueous solution, stir evenly and ultrasonically disperse for 10 minutes, add the initiator aqueous solution when the water bath is heated to 70-80°C, add dropwise the acrylate monomer and the remaining initiator After the dropwise addition, the reaction was continued for 5 hours, cooled naturally to room temperature, and filtered to obtain a uniform and stable nano-titanium dioxide graft copolymer.
[0014] In the nano-titanium dioxide graft copolymer, in ...
Embodiment 1
[0032] (1) Preparation of Nano Titanium Dioxide Graft Copolymer
[0033] a. Weigh 15 parts of nano-titanium dioxide particles and 2 parts of silane coupling agent in 150 mL of absolute ethanol, stir evenly and disperse ultrasonically for 10 minutes, heat in a water bath to 50°C for 5 hours, dry at 80°C and grind to obtain modification Nano titanium dioxide particles; the silane coupling agent is γ-methacryloxypropyltrimethoxysilane (KH-570).
[0034]b. Add the modified nano-titanium dioxide particles to a solution of 12 parts of polymerizable emulsifier and 300mL of water, stir evenly and then ultrasonically disperse for 10 minutes. When the water bath is heated to 70°C, add 0.5 parts of an aqueous solution of initiator potassium persulfate, dropwise The aqueous solution of 54 parts of acrylate monomer, 14 parts of fluorine-containing monomer and 0.5 part of initiator potassium persulfate, continued to react for 5 hours after the dropwise addition, naturally cooled to room tem...
Embodiment 2
[0042] (1) Preparation of Nano Titanium Dioxide Graft Copolymer
[0043] a. Weigh 17 parts of nano-titanium dioxide particles and 3 parts of silane coupling agent in 200mL of absolute ethanol, stir evenly and then ultrasonically disperse for 10 minutes, heat in a water bath to 60°C for 5 hours, dry at 80°C and grind to obtain modification Nano titanium dioxide particles; the silane coupling agent is vinyltriethoxysilane (KH-151).
[0044] b. Add the modified nano-titanium dioxide particles to a solution of 15 parts of polymerizable emulsifier and 300mL of water, stir evenly and ultrasonically disperse for 10 minutes. When the water bath is heated to 75°C, add 0.5 parts of the aqueous solution of initiator ammonium persulfate, dropwise The aqueous solution of 61 parts of acrylate monomer, 18 parts of fluorine-containing monomer and 0.7 part of initiator ammonium persulfate, continued to react for 5 hours after the dropwise addition, cooled naturally to room temperature, and fil...
PUM
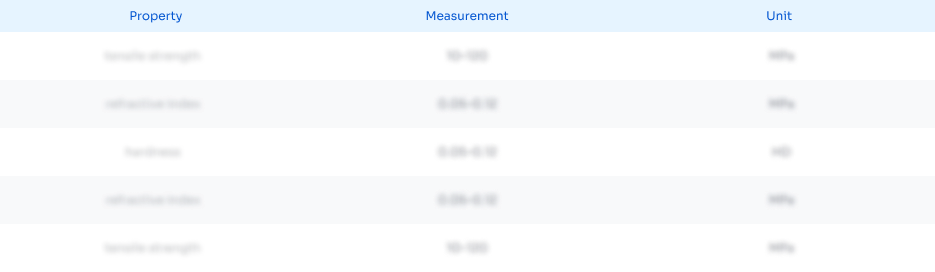
Abstract
Description
Claims
Application Information

- R&D
- Intellectual Property
- Life Sciences
- Materials
- Tech Scout
- Unparalleled Data Quality
- Higher Quality Content
- 60% Fewer Hallucinations
Browse by: Latest US Patents, China's latest patents, Technical Efficacy Thesaurus, Application Domain, Technology Topic, Popular Technical Reports.
© 2025 PatSnap. All rights reserved.Legal|Privacy policy|Modern Slavery Act Transparency Statement|Sitemap|About US| Contact US: help@patsnap.com