Cr-Ni alloy electroplating liquid and electroplating method
An alloy electroplating solution and technology of electroplating solution, applied in the field of electroplating solution, can solve the problems of insufficient dispersing ability and deep plating ability of electroplating solution, complicated formula, poor hardness and corrosion resistance of coating layer, etc.
- Summary
- Abstract
- Description
- Claims
- Application Information
AI Technical Summary
Problems solved by technology
Method used
Image
Examples
Embodiment 1
[0029] The formula of Cr-Ni alloy electroplating solution is as follows:
[0030] Table 1-1 Cr-Ni alloy electroplating solution
[0031]
[0032] Plating process conditions: the frequency of square wave pulse current is 100Hz, the duty cycle is 15%, and the average current density is 10A / dm 2 ; The pH is 2, the temperature is 30° C., and the time is 80 minutes.
Embodiment 2
[0034] The formula of Cr-Ni alloy electroplating solution is as follows:
[0035] Table 2-1 Cr-Ni alloy electroplating solution
[0036]
[0037] Plating process conditions: the frequency of square wave pulse current is 1000Hz, the duty cycle is 30%, and the average current density is 30A / dm 2 ; The pH is 4, the temperature is 60° C., and the time is 250 minutes.
Embodiment 3
[0039]The formula of Cr-Ni alloy electroplating solution is as follows:
[0040] Table 3-1 Cr-Ni alloy electroplating solution
[0041]
[0042] Plating process conditions: the frequency of square wave pulse current is 650Hz, the duty cycle is 25%, and the average current density is 20A / dm 2 ; The pH is 3, the temperature is 45° C., and the time is 160 minutes.
PUM
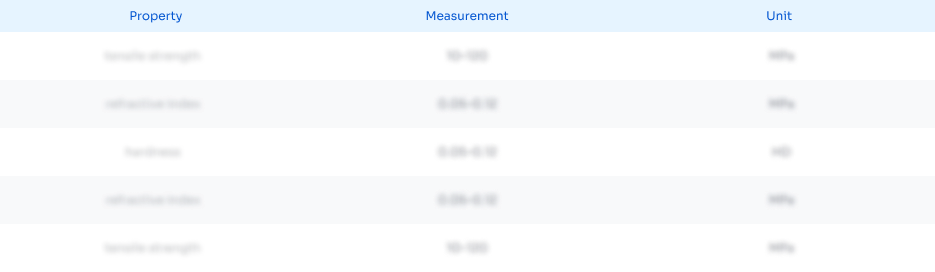
Abstract
Description
Claims
Application Information

- R&D
- Intellectual Property
- Life Sciences
- Materials
- Tech Scout
- Unparalleled Data Quality
- Higher Quality Content
- 60% Fewer Hallucinations
Browse by: Latest US Patents, China's latest patents, Technical Efficacy Thesaurus, Application Domain, Technology Topic, Popular Technical Reports.
© 2025 PatSnap. All rights reserved.Legal|Privacy policy|Modern Slavery Act Transparency Statement|Sitemap|About US| Contact US: help@patsnap.com