Vulnerable part of welding gun and surface treatment method of vulnerable part
A technology for surface treatment and wearing parts, applied in welding equipment, auxiliary welding equipment, welding/cutting auxiliary equipment, etc., can solve the problem of softening and deformation of copper wearing parts, easy slag hanging and burning, and difficulty in cleaning copper materials and other problems, to achieve the effect of solving the burning deformation, not easy to foam, and reducing the phenomenon of slag hanging
- Summary
- Abstract
- Description
- Claims
- Application Information
AI Technical Summary
Problems solved by technology
Method used
Image
Examples
Embodiment 1
[0033] See figure 1 , the present embodiment takes the nozzle as an example to illustrate the structure and surface treatment method of the wearing parts of the present invention, figure 1 The middle is the composite nozzle.
[0034] figure 1 The nozzle in the nozzle is a hollow structure, including an outer shell 11, an insulating layer 12 and an inner core 13, wherein the outer shell 11 and the inner core 13 are made of copper. The insulating layer 12 is arranged on the inner wall of the casing 11 away from the injection hole. The outer surface 111 of the nozzle and the exposed inner surface 112 of the nozzle are coated with a metal oxide coating (not shown), and the metal oxide coating is 89-91% zirconium dioxide powder and 9-11% trioxide Two aluminum powders make the nozzle of this embodiment have good heat resistance, wear resistance and hardness, the melting point reaches 2800 degrees Celsius, and the thermal shock resistance reaches 450 degrees Celsius. service life...
Embodiment 2
[0042] See figure 2 , the present embodiment takes the nozzle as an example to illustrate the structure and surface treatment method of the wearing parts of the present invention, figure 2 One-piece nozzle. The outer surface 111 of the nozzle is coated with a metal oxide coating (not shown in the figure), and the exposed inner surface 112 of the nozzle may also be coated with a metal oxide coating.
Embodiment 3
[0044] See image 3 , this embodiment takes the contact tip as an example to illustrate the structure and surface treatment method of the consumable parts of the present invention. like image 3 As shown, the contact tip is a copper hollow structure, including the outer surface 21 of the contact tip and the inner surface 22 of the contact tip. The outer surface 21 of the contact tip is coated with a metal oxide coating (not shown in the figure), and the inner surface of the contact tip Surface 22 may also be coated with a metal oxide coating.
PUM
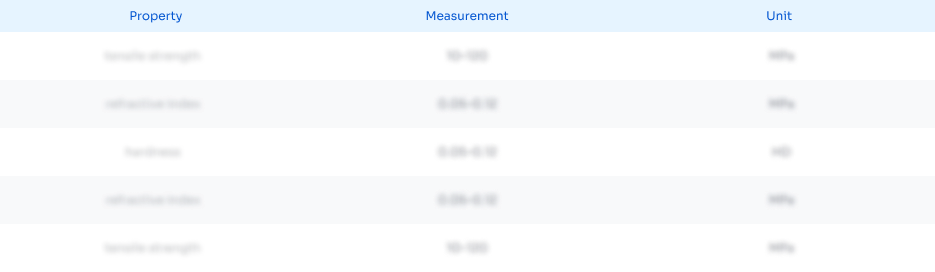
Abstract
Description
Claims
Application Information

- R&D
- Intellectual Property
- Life Sciences
- Materials
- Tech Scout
- Unparalleled Data Quality
- Higher Quality Content
- 60% Fewer Hallucinations
Browse by: Latest US Patents, China's latest patents, Technical Efficacy Thesaurus, Application Domain, Technology Topic, Popular Technical Reports.
© 2025 PatSnap. All rights reserved.Legal|Privacy policy|Modern Slavery Act Transparency Statement|Sitemap|About US| Contact US: help@patsnap.com