Molybdenum alloy lubricant additive and preparation method thereof
A lubricating oil additive, molybdenum alloy technology, applied in additives, lubricating compositions, petroleum industry, etc., can solve problems such as extreme pressure load, unsatisfactory anti-corrosion performance, and unsatisfactory performance, and achieve significant fuel-saving effect and good lubrication performance, excellent anti-wear effect
- Summary
- Abstract
- Description
- Claims
- Application Information
AI Technical Summary
Problems solved by technology
Method used
Examples
preparation example Construction
[0014] The preparation method of the molybdenum alloy lubricating oil additive of the present invention is based on coconut oil and reacts with triethanolamine, then adds methyl laurate, adopts the method for adjusting the pH value to obtain mixed amide, and then reacts with sodium molybdate, boric acid, tungsten oxide Reaction, adopt two-step pressure method under the situation of adding polyenoic acid polyamine, polyethylene glycol, make molybdenum alloy lubricating oil additive, step is as follows:
[0015] 1) Synthesis of mixed amides
[0016] Put coconut oil and triethanolamine in a container, and react at 100°C to 110°C for 2 to 3 hours under nitrogen protection, then add methyl laurate, adjust the pH to 9 to 10, and increase the temperature to 110°C to 120°C. Continue to react for 4 to 5 hours to obtain a mixed amide, the mass ratio of coconut oil: triethanolamine: methyl laurate = 2 to 3: 3 to 4: 1 to 1.5;
[0017] 2) Synthesis of molybdenum alloy lubricating oil addi...
Embodiment 1
[0029] 1. Synthesis of mixed amides
[0030] Put coconut oil and triethanolamine in a container, react at 100°C for 2 hours under nitrogen protection, then adjust the pH to 10 with oleic acid methyl ester, and continue the reaction at 110°C for 4 hours to obtain a mixed amide;
[0031] Coconut oil: triethanolamine: methyl laurate=2:3:1 (weight ratio).
[0032] 2. Synthesis of molybdenum alloy lubricating oil additives
[0033] Mix 50 grams of the mixed amide prepared above with 4.5 grams of sodium molybdate, 3 grams of boric acid, and 4.5 grams of tungsten oxide. After stirring evenly, add 5.5 grams of polyenoic acid polyamine, and react at a temperature of 90°C and a negative pressure of 100mmHg for 4 hour; then add 6 grams of polyethylene glycol, increase the temperature to 180°C, and continue the reaction for 3 hours under a negative pressure of 70mmHg. Then lower the temperature to 100°C, evacuate to a pressure of 0.097MPa, and extract low-boiling substances; finally fil...
Embodiment 2
[0036] 1. Synthesis of mixed amides
[0037] Put coconut oil and triethanolamine in a container and react at 110°C for 3 hours under nitrogen protection, then add oleic acid methyl ester, adjust the pH to 9, and continue the reaction at 120°C for 5 hours to obtain a mixed amide;
[0038] Coconut oil: triethanolamine: methyl laurate=2:3:1 (weight ratio).
[0039] 2. Synthesis of molybdenum alloy lubricating oil additives
[0040] Mix 100 grams of the mixed amide prepared above with 8 grams of sodium molybdate, 6.5 grams of boric acid, and 8 grams of tungsten oxide. After stirring evenly, add 12 grams of polyenoic acid polyamine, and react at a temperature of 95 ° C and a negative pressure of 100 mmHg for 5 hour; then add 14 grams of polyethylene glycol, increase the temperature to 190°C, and continue the reaction for 4 hours under the high condition of negative pressure 70mmHg. Then lower the temperature to 100°C, evacuate to a pressure of 0.097MPa, and extract low-boiling su...
PUM
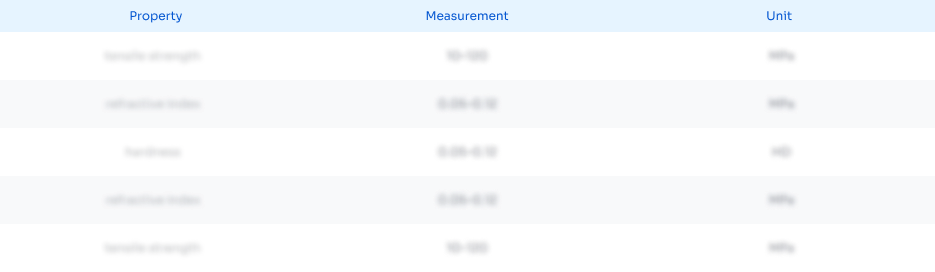
Abstract
Description
Claims
Application Information

- R&D
- Intellectual Property
- Life Sciences
- Materials
- Tech Scout
- Unparalleled Data Quality
- Higher Quality Content
- 60% Fewer Hallucinations
Browse by: Latest US Patents, China's latest patents, Technical Efficacy Thesaurus, Application Domain, Technology Topic, Popular Technical Reports.
© 2025 PatSnap. All rights reserved.Legal|Privacy policy|Modern Slavery Act Transparency Statement|Sitemap|About US| Contact US: help@patsnap.com