Preparation method for ammonium polyphosphate/kaolin composite flame retardant
A technology of compound flame retardant and ammonium polyphosphate, which is used in the field of non-metallic mineral deep processing materials and halogen-free flame retardant materials, can solve the problem of unsatisfactory dialysis effect of ammonium polyphosphate, difficult coating and microencapsulation and microencapsulation. Surface damage and other problems, to achieve the effect of improving anti-dialysis performance, good machinability and low cost
- Summary
- Abstract
- Description
- Claims
- Application Information
AI Technical Summary
Problems solved by technology
Method used
Image
Examples
Embodiment 1
[0016] Take granularity D 97 Calcined 80g of ultrafine water-washed kaolin <10μm in a muffle furnace at 800°C for 1.5h to obtain calcined kaolin; take 200g of ammonium polyphosphate and modify its surface with 30g of melamine at 200°C for 1.5h , to obtain modified ammonium polyphosphate; after uniformly mixing 50 g of calcined kaolin and 150 g of modified ammonium polyphosphate, 3 g of simethicone oil was added at 105 ° C for surface modification, and the modification time was 30 minutes to obtain ammonium polyphosphate / Kaolin composite flame retardant.
[0017] Add the prepared ammonium polyphosphate / kaolin composite flame retardant to EVA cable material to make a sample of flame retardant sheath material. The formula is: 45 parts of composite flame retardant, 50 parts of EVA, antioxidant, compatibilizer, lubricant There are 5 parts of agent and color masterbatch. According to the following methods and standards, the dialysis rate and oxygen index change rate performance i...
Embodiment 2
[0027] Take granularity D 97 60g of ultra-fine water-washed kaolin <10μm was calcined in a muffle furnace at 900°C for 1h to obtain calcined kaolin; take 200g of ammonium polyphosphate and modify its surface with 10g of melamine at 150°C for 1.5h. Obtain modified ammonium polyphosphate; after uniformly mixing 40 g of calcined kaolin and 160 g of modified ammonium polyphosphate, add 4 g of hydroxyl silicone oil at 120° C. Fuel.
[0028]The preparation and performance measurement methods of the flame retardant sheath material samples are the same as in Example 1.
[0029] The test results of the performance indicators of the dialysis rate and oxygen index change rate of the sheath material samples are listed in Table 1.
Embodiment 3
[0031] Take granularity D 97 50g of ultra-fine water-washed kaolin <10μm was calcined in a muffle furnace at 600°C for 1.5h to obtain calcined kaolin; take 200g of ammonium polyphosphate and modify its surface with 40g of melamine at 120°C for 1h. Obtain modified ammonium polyphosphate; after uniformly mixing 25g of calcined kaolin and 125g of modified ammonium polyphosphate, add 3g of γ-methacryloxypropyltrimethoxysilane at 80°C for surface modification, and the modification time 30min, the ammonium polyphosphate / kaolin composite flame retardant was prepared.
[0032] The preparation and performance measurement methods of the flame retardant sheath material samples are the same as in Example 1.
[0033] The test results of the performance indicators of the dialysis rate and the oxygen index change rate of the sheath material samples are listed in Table 1.
PUM
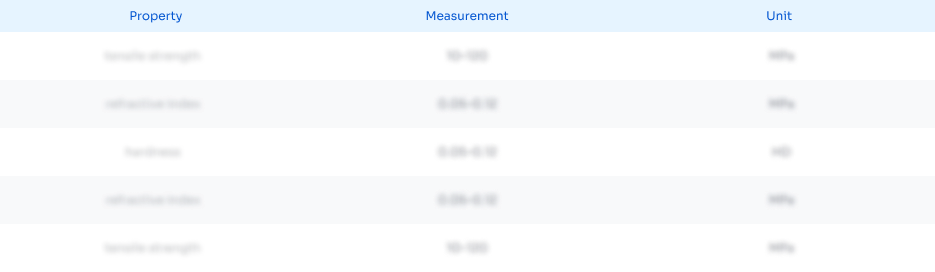
Abstract
Description
Claims
Application Information

- R&D Engineer
- R&D Manager
- IP Professional
- Industry Leading Data Capabilities
- Powerful AI technology
- Patent DNA Extraction
Browse by: Latest US Patents, China's latest patents, Technical Efficacy Thesaurus, Application Domain, Technology Topic, Popular Technical Reports.
© 2024 PatSnap. All rights reserved.Legal|Privacy policy|Modern Slavery Act Transparency Statement|Sitemap|About US| Contact US: help@patsnap.com