Preparation method of high-strength wear resistant polyester harness
A manufacturing method and high-strength technology, applied in the direction of textiles and papermaking, textile material processing, continuous processing of textile materials, etc., can solve problems such as fabric warp defects, through-filament breakage, and large through-filament stretching, and achieve high-quality products. Enhanced breaking strength, improved coefficient of friction, and improved wear resistance
- Summary
- Abstract
- Description
- Claims
- Application Information
AI Technical Summary
Problems solved by technology
Method used
Examples
Embodiment 1
[0022] A kind of manufacture method of high-strength wear-resistant polyester through-filament, it comprises the following steps:
[0023] 1) Doubling, merging 1 hose polyester yarn and 2 polyester filter tows into 1 strand;
[0024] 2) Initial twist, twist direction Z, number of strands twist is twist / 100cm;
[0025] 3) Double twisting, the twist direction is S, the number of strands and the twist is 100㎝;
[0026] 4) stranded wire, with the twisted strand in (3), is wound into stranded wire by the yarn reeling machine;
[0027] 5) Then put the polyester stranded wire into the slurry for dipping, and the raw material parts by weight of the slurry are as follows:
[0028] 50 parts of polyvinyl alcohol, 5 parts of polyoxyethylene ether penetrant, 50 parts of water; the concentration of the slurry is 5%, the soaking time is 3 hours, and sizing at room temperature;
[0029] 6) dehydration, step 5) sizing the good polyester strands, remove 70% slurry by dehydrator;
[0030] 7)...
PUM
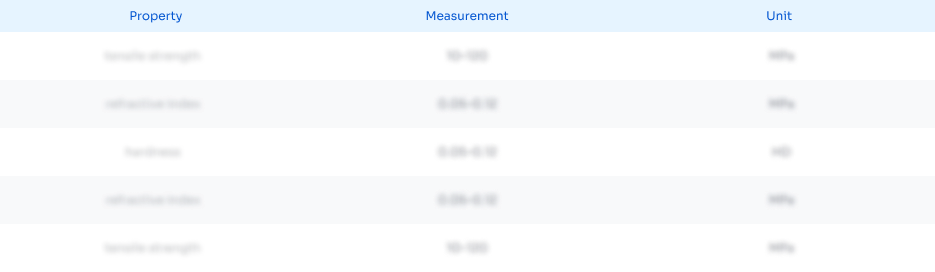
Abstract
Description
Claims
Application Information

- Generate Ideas
- Intellectual Property
- Life Sciences
- Materials
- Tech Scout
- Unparalleled Data Quality
- Higher Quality Content
- 60% Fewer Hallucinations
Browse by: Latest US Patents, China's latest patents, Technical Efficacy Thesaurus, Application Domain, Technology Topic, Popular Technical Reports.
© 2025 PatSnap. All rights reserved.Legal|Privacy policy|Modern Slavery Act Transparency Statement|Sitemap|About US| Contact US: help@patsnap.com