Clearing device and method used for aluminum-zinc pot molten pool bottom slag
A cleaning device and molten pool technology, applied in the coating, metal material coating process, hot-dip coating process, etc., can solve the problem of long downtime, increased bottom slag in the aluminum-zinc pot molten pool, and affecting the flow of the aluminum-zinc pot molten pool Field distribution and other issues, to achieve the effect of convenient use
- Summary
- Abstract
- Description
- Claims
- Application Information
AI Technical Summary
Problems solved by technology
Method used
Image
Examples
Embodiment 1
[0028] The invention discloses a device for crushing the bottom slag of an aluminum-zinc pot melting pool, which mainly consists of a punch 1, a connecting seat 2, a support rod 3, a bearing seat 4, an impact body traction ring 5, an impact body 6, and a support rod suspension ring 7 composition.
[0029] The main body of the punch 1 is a cylinder with a diameter of 55-65 mm, and the material is 45 steel. The high-temperature-resistant and aluminum-zinc corrosion-resistant cone blank is surfacing on one end of the punch 1 by surfacing welding. The surfacing material is stellite6 cobalt-based alloy. Material, preheat the base metal of the punch to 250~350°C before surfacing, cover with refractory fiber and cool slowly to room temperature after surfacing, and then turn the cone blank on a lathe with a cemented carbide tool, the cone angle is controlled In the range of 60~120o, the cone tip fillet radius is 3~10 mm. The number of punches 1 is 1-3. The length of punch 1 is 250~3...
Embodiment 2
[0050] The invention discloses a device for crushing the bottom slag of an aluminum-zinc pot melting pool, which mainly consists of a punch 1, a connecting seat 2, a support rod 3, a bearing seat 4, an impact body traction ring 5, an impact body 6, and a support rod suspension ring 7 composition.
[0051] The main body of the punch 1 is a cylinder with a diameter of 55-65 mm, and the material is 40CrMo medium-carbon low-alloy round steel. The high-temperature-resistant and aluminum-zinc corrosion-resistant cone blank is surfacing on one end of the punch 1 by surfacing welding. It is a stellite6 cobalt-based alloy material. Before surfacing, preheat the base metal of the punch to 250~350°C. After surfacing, cover it with refractory fiber and slowly cool it to room temperature. Then use a carbide tool to turn the cone blank on a lathe. The cone angle of the body is controlled in the range of 60~120o, and the radius of the cone tip fillet is 3~10 mm. The number of punches 1 is 1...
Embodiment 3
[0069] The invention discloses a device for crushing the bottom slag of an aluminum-zinc pot melting pool, which mainly consists of a punch 1, a connecting seat 2, a support rod 3, a bearing seat 4, an impact body traction ring 5, an impact body 6, and a support rod suspension ring 7 composition.
[0070] The main body of the punch 1 is a cylinder with a diameter of 55-65 mm, and the material is 38CrNiMo medium-carbon low-alloy round steel. The high-temperature-resistant and aluminum-zinc corrosion-resistant cone blank is surfacing on one end of the punch 1 by surfacing welding. It is a stellite6 cobalt-based alloy material. Before surfacing, preheat the base metal of the punch to 250~350°C. After surfacing, cover it with refractory fiber and slowly cool it to room temperature. Then use a carbide tool to turn the cone blank on a lathe. The cone angle of the body is controlled in the range of 60~120o, and the radius of the cone tip fillet is 3~10 mm. The number of punches 1 is...
PUM
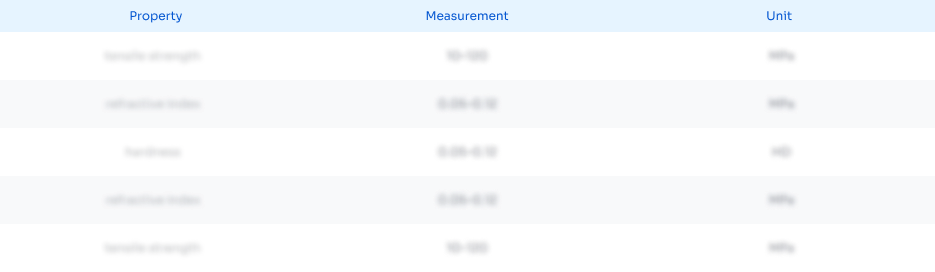
Abstract
Description
Claims
Application Information

- R&D
- Intellectual Property
- Life Sciences
- Materials
- Tech Scout
- Unparalleled Data Quality
- Higher Quality Content
- 60% Fewer Hallucinations
Browse by: Latest US Patents, China's latest patents, Technical Efficacy Thesaurus, Application Domain, Technology Topic, Popular Technical Reports.
© 2025 PatSnap. All rights reserved.Legal|Privacy policy|Modern Slavery Act Transparency Statement|Sitemap|About US| Contact US: help@patsnap.com