Strong basic composite resin material and preparation method thereof
A composite resin and strong alkaline technology, which is applied in the field of strong alkaline composite resin materials and their preparation, can solve the problems of uneven dispersion of nanomaterials, poor heat resistance of resins, poor swelling resistance, etc., and achieve simple preparation process, Effect of smooth surface topography, good thermal stability and swelling resistance
- Summary
- Abstract
- Description
- Claims
- Application Information
AI Technical Summary
Problems solved by technology
Method used
Image
Examples
Embodiment 1
[0045] Get 53.5 grams of p-chloromethylstyrene, 6.6 grams of divinylbenzene, 0.3 grams of benzoyl peroxide initiator and 2.2 grams of carboxylated graphene, and after uniform mixing, use 40 kHz ultrasonic vibration for 20 minutes to obtain a black uniform dispersion (The suspension is still uniformly dispersed without sediment after standing for 10 minutes, which proves that the functionalized graphene can maintain a high degree of dispersion in the polymerized monomer). The above-mentioned dispersion liquid was poured into a 250 ml three-necked flask, and stirred at 60° C. for 2 hours to carry out prepolymerization. 130 mL of deionized water in which 1.3 g of polyvinyl alcohol had been dissolved was added. Gradually raise the temperature to 80°C and react for 5 hours; then raise the temperature to 90°C and react for 5 hours; finally raise the temperature to 98°C and react for 6 hours. After the reaction, pour out the upper liquid, wash it with hot water, then filter it, put ...
Embodiment 2
[0049] Take 135.5 grams of 4-(4-chlorobutyl) styrene, 8.0 grams of divinylbenzene, 1.0 grams of benzoyl peroxide initiator and 3.2 grams of hydroxylated graphene, and use 60 kHz ultrasonic vibration for 15 minutes after uniform mixing to obtain Black homogeneous dispersion (the suspension is still uniformly dispersed without sediment after standing for 10 minutes, which proves that the functionalized graphene can maintain a high degree of dispersion in the polymerized monomer). Pour the dispersion into a 500 ml three-neck flask, add 3.0 g of gelatin and 250 ml of deionized water, stir to dissolve all the gelatin, then gradually raise the temperature, react at 75°C for 5 hours, heat up to 85°C for 5 hours, and then heat up React at 92°C for 4 hours, and finally raise the temperature to 100°C for 6 hours. After the reaction, pour out the upper liquid, wash with hot water, filter, put in an oven to dry at 80°C, and sieve to collect composite microspheres B with a particle size in...
Embodiment 3
[0053] Get 237 grams of p-chloromethyl styrene, 13.9 grams of dipenylbenzene, 3.0 grams of azobisisobutyronitrile initiator and 4.2 grams of primary aminated graphene, and after uniform mixing, use 75 kHz ultrasonic vibration for 10 minutes to obtain a uniform black Dispersion liquid (the suspension is still uniformly dispersed without sediment after standing for 10 minutes, which proves that the functionalized graphene can maintain a high degree of dispersion in the polymerized monomer). The above-mentioned dispersion liquid was added into a 1000 ml three-necked flask, and stirred at 65° C. for 1.5 hours to carry out prepolymerization. Then 500 ml of deionized water in which 5.0 g of gelatin had been dissolved was added. The temperature was raised to 80°C within 1 hour, and the reaction was continued for 5 hours; the temperature was then raised to 90°C, and the reaction was continued for 6 hours, and finally the temperature was raised to 98°C, and the reaction was continued f...
PUM
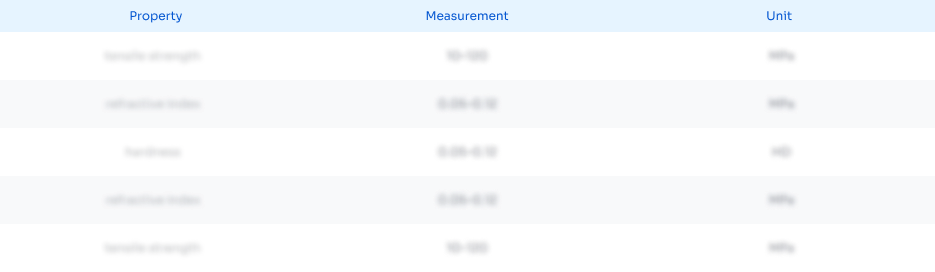
Abstract
Description
Claims
Application Information

- Generate Ideas
- Intellectual Property
- Life Sciences
- Materials
- Tech Scout
- Unparalleled Data Quality
- Higher Quality Content
- 60% Fewer Hallucinations
Browse by: Latest US Patents, China's latest patents, Technical Efficacy Thesaurus, Application Domain, Technology Topic, Popular Technical Reports.
© 2025 PatSnap. All rights reserved.Legal|Privacy policy|Modern Slavery Act Transparency Statement|Sitemap|About US| Contact US: help@patsnap.com