Induction-cladded gradient hard composite material coating technique
A composite material, hard technology, applied in the direction of metal material coating process, coating, fusion spraying, etc., can solve the problems of coating hard phase growth, Cokendall diffusion pores, restrictions, etc., to improve resistance The ability of thermal shock, avoiding the deterioration of matrix structure, and the effect of simple preparation method
- Summary
- Abstract
- Description
- Claims
- Application Information
AI Technical Summary
Problems solved by technology
Method used
Examples
Embodiment 1
[0014] Utilize the present invention to prepare 600 μm thick gradient hard composite material coating with WC hard phase and Ni-based self-fluxing alloy on the surface of AISI 304L austenitic stainless steel plate parts. The preparation steps are as follows: first, the spray drying method is used to prepare WC Three kinds of composite spraying powder with hard phase volume percentage of 0%, 25% and 50%; do routine cleaning treatment on the surface of AISI 304L stainless steel substrate to be treated, remove surface oil and impurities, and use 60 mesh corundum sand for 10 seconds / cm 2;Using the oxyacetylene flame spraying method, three kinds of composite spraying powders with WC hard phase volume percentage of 0%, 25% and 50% were sprayed layer by layer, and a 3-sublayer structure prefabricated with each sublayer thickness of 200 μm was obtained. Coating: use a rectangular induction coil 5 mm larger than the width of the part to scan and heat cladding, the output power of the ...
Embodiment 2
[0016] Utilize the present invention to prepare 450 μm thick with Cr 3 C 2 Gradient hard composite coating of hard phase and NiCr metal phase, the preparation steps are as follows: first, adopt the spray drying method to prepare Cr 3 C 2 Three kinds of composite powders with hard phase volume percentages of 20%, 40% and 80%; do conventional cleaning treatment on the surface of SA182M-F304 stainless steel substrate to be treated, remove surface oil and impurities, and use 60 mesh corundum sand for 10 seconds / cm 2 ; Using oxyacetylene flame flame spraying method, spraying Cr layer by layer 3 C 2 Three kinds of composite powders with hard phase volume percentage of 20%, 40% and 80% were used to obtain a three-sub-layer structure pre-coating with each sub-layer thickness of 150 μm; a circular induction coil with an inner diameter of 104 mm was used to induce The output power of the power supply is 100 kW, the frequency is 60 kHz, and the maximum current is 2500 A. The sphere...
Embodiment 3
[0018] Utilize the present invention to prepare on the 17-4PH martensitic stainless steel cylinder part of diameter 30mm, length 100mm, have 360 μ m thick graded hard composite material coating with WC hard phase and Ni base self-fluxing alloy, preparation steps are as follows : Firstly adopt spray drying method to prepare two kinds of composite spraying powders with WC hard phase volume percentage of 35% and 85%; do routine cleaning treatment on the surface to be treated of 17-4PH martensitic stainless steel substrate to remove surface oil and impurities, Use 46 mesh corundum sand blasting treatment for 10 seconds / cm 2 ;Using the supersonic spraying method, two kinds of composite powders with WC hard phase volume percentages of 35% and 85% were sprayed and deposited respectively, and the first sub-layer thickness was 120 μm, and the second sub-layer thickness was 240 μm. Sub-layer structure pre-coating; using a circular induction coil with an inner diameter of 36 mm, the ou...
PUM
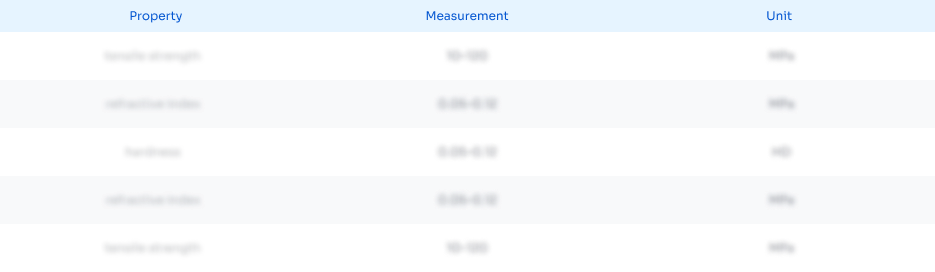
Abstract
Description
Claims
Application Information

- Generate Ideas
- Intellectual Property
- Life Sciences
- Materials
- Tech Scout
- Unparalleled Data Quality
- Higher Quality Content
- 60% Fewer Hallucinations
Browse by: Latest US Patents, China's latest patents, Technical Efficacy Thesaurus, Application Domain, Technology Topic, Popular Technical Reports.
© 2025 PatSnap. All rights reserved.Legal|Privacy policy|Modern Slavery Act Transparency Statement|Sitemap|About US| Contact US: help@patsnap.com