Friction-resistant plastic and preparation method thereof
A friction-resistant and plastic technology, applied in the field of plastic products, can solve the problems of poor friction resistance, restricting the development of plastics, and short service life, etc., and achieve the effects of high production efficiency, enhanced chemical stability, and convenient operation
- Summary
- Abstract
- Description
- Claims
- Application Information
AI Technical Summary
Problems solved by technology
Method used
Examples
Embodiment 1
[0023] A friction-resistant plastic provided in this embodiment, the composition of the friction-resistant plastic is as follows: polyvinyl chloride resin: 90 parts, silicon carbide: 6 parts, talcum powder: 1 part, graphite powder: 5 parts, double Phenol A epoxy resin: 50 parts, sodium tripolyphosphate: 5 parts, mineral oil: 3 parts, polyvinylidene chloride: 7 parts, sodium tripolyphosphate: 7 parts, hydroxypropyl methacrylate: 6 parts, titanium White powder: 1 part, iron powder: 5 parts, deionized water: 30 parts, silane coupling agent KH560: 3 parts, auxiliary agent: 2 parts;
[0024] The components of the additives are calculated in parts by weight: mica powder: 3 parts, kaolinite: 1 part, deionized water: 50 parts, glycerin: 5 parts, calcium oxide: 1 part, magnesium hydroxide: 4 parts, Paraffin: 1 part, polyvinyl chloride resin: 12 parts;
[0025] The preparation method of the auxiliary agent is: mix and pulverize mica powder, kaolinite, glycerin, and calcium oxide, pass ...
Embodiment 2
[0031] A friction-resistant plastic provided in this embodiment, the components of the friction-resistant plastic are: polyvinyl chloride resin: 92 parts, silicon carbide: 8 parts, talcum powder: 3 parts, graphite powder: 7 parts, double Phenol A epoxy resin: 55 parts, sodium tripolyphosphate: 10 parts, mineral oil: 5 parts, polyvinylidene chloride: 9 parts, sodium tripolyphosphate: 9 parts, hydroxypropyl methacrylate: 8 parts, titanium White powder: 3 parts, iron powder: 7 parts, deionized water: 40 parts, silane coupling agent KH560: 5 parts, additives: 4 parts;
[0032]The components of the auxiliary agent are calculated in parts by weight: mica powder: 5 parts, kaolinite: 3 parts, deionized water: 60 parts, glycerin: 7 parts, calcium oxide: 3 parts, magnesium hydroxide: 6 parts, Paraffin: 3 parts, polyvinyl chloride resin: 14 parts;
[0033] The preparation method of the auxiliary agent is: mix and pulverize mica powder, kaolinite, glycerin, and calcium oxide, pass throug...
Embodiment 3
[0039] A friction-resistant plastic provided in this embodiment, the components of the friction-resistant plastic are: polyvinyl chloride resin: 91 parts, silicon carbide: 7 parts, talcum powder: 2 parts, graphite powder: 6 parts, double Phenol A epoxy resin: 54 parts, sodium tripolyphosphate: 8 parts, mineral oil: 4 parts, polyvinylidene chloride: 8 parts, sodium tripolyphosphate: 8 parts, hydroxypropyl methacrylate: 7 parts, titanium White powder: 2 parts, iron powder: 6 parts, deionized water: 35 parts, silane coupling agent KH560: 4 parts, additives: 3 parts;
[0040] The components of the auxiliary agent are calculated in parts by weight: mica powder: 4 parts, kaolinite: 2 parts, deionized water: 56 parts, glycerin: 6 parts, calcium oxide: 2 parts, magnesium hydroxide: 5 parts, Paraffin: 2 parts, polyvinyl chloride resin: 13 parts;
[0041] The preparation method of the auxiliary agent is: mix and pulverize mica powder, kaolinite, glycerin, and calcium oxide, pass throug...
PUM
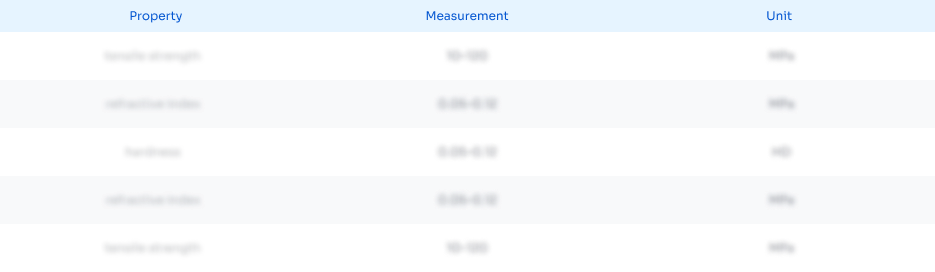
Abstract
Description
Claims
Application Information

- R&D
- Intellectual Property
- Life Sciences
- Materials
- Tech Scout
- Unparalleled Data Quality
- Higher Quality Content
- 60% Fewer Hallucinations
Browse by: Latest US Patents, China's latest patents, Technical Efficacy Thesaurus, Application Domain, Technology Topic, Popular Technical Reports.
© 2025 PatSnap. All rights reserved.Legal|Privacy policy|Modern Slavery Act Transparency Statement|Sitemap|About US| Contact US: help@patsnap.com