Method for extracting high-purity uranium, thorium and mixed rare earths from excellent molten slag
A mixed rare earth and molten slag technology, applied in the field of extracting high-purity uranium, thorium and mixed rare earth, can solve the problems of low industrial utilization value, large acid consumption in leaching of nitric acid system, complicated technological process, etc., and achieve obvious social benefits and Economic benefits, easy mass production, simple process effect
- Summary
- Abstract
- Description
- Claims
- Application Information
AI Technical Summary
Problems solved by technology
Method used
Image
Examples
Embodiment 1
[0021] The ratio of monazite excellent slag (kg): hydrochloric acid (L)=1:8 was added in the hydrochloric acid solution of 0.35mol / L, stirred at room temperature for 4 hours, clarified for 2 hours, and the siphon supernatant was obtained containing uranium, thorium and rare earth solution. Put the slurry after siphoning the supernatant into the plate and frame filter press with a pump, press filter until no solution flows out, and combine the filtrate with the supernatant in step 1. The filter residue of the plate and frame press is washed with water until the pH value of the filtrate is 2.0 to 3.0, and the washing liquid is combined with the supernatant in step 1 to obtain a clarified aqueous solution and filter residue containing uranium, thorium and rare earth (the leaching rate of uranium in the slag is 82 %, the leaching rate of thorium is 89%, and the leaching rate of rare earth is 62%).
[0022] With the concentration of 15% dimethylheptyl phosphate as the extractant, ...
Embodiment 2
[0033] Add monazite excellent slag (kg): hydrochloric acid (L)=1:8 in the hydrochloric acid solution of 0.5mol / L, stir at room temperature for 6 hours, clarify for 2 hours, siphon the supernatant to obtain uranium, thorium and rare earth solution. Put the slurry after siphoning the supernatant into the plate and frame filter press with a pump, press filter until no solution flows out, and combine the filtrate with the supernatant in step 1. The filter residue of the plate and frame press is washed with water until the pH value of the filtrate is 2.0 to 3.0, and the washing liquid is combined with the supernatant in step 1 to obtain a clarified aqueous solution and filter residue containing uranium, thorium and rare earth (the leaching rate of uranium in the slag is 90 %, the leaching rate of thorium is 92%, and the leaching rate of rare earth is 71%).
[0034] With the concentration of 20% dimethylheptyl methyl phosphate as the extraction agent, the extraction ratio is 2:1, a...
Embodiment 3
[0038] The ratio of monazite molten slag (kg):hydrochloric acid (L)=1:10 was added in the hydrochloric acid solution of 0.8mol / L, stirred at room temperature for 8 hours, clarified for 4 hours, siphoned the supernatant to obtain uranium, thorium and rare earth solution. Put the slurry after siphoning the supernatant into the plate and frame filter press with a pump, press filter until no solution flows out, and combine the filtrate with the supernatant in step 1. The filter residue of the plate and frame press is washed with water until the pH value of the filtrate is 2.0 to 3.0, and the washing liquid is combined with the supernatant in step 1 to obtain a clarified aqueous solution and filter residue containing uranium, thorium and rare earth (the leaching rate of uranium in the slag is 93 %, the leaching rate of thorium is 95%, and the leaching rate of rare earth is 84%).
[0039] With a concentration of 25% dimethylheptyl phosphate as the extraction agent, the extraction r...
PUM
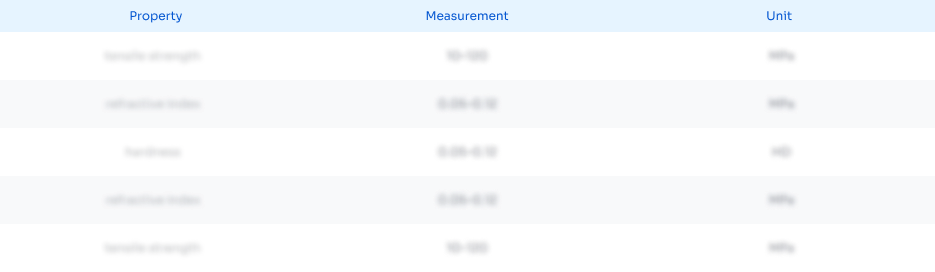
Abstract
Description
Claims
Application Information

- R&D
- Intellectual Property
- Life Sciences
- Materials
- Tech Scout
- Unparalleled Data Quality
- Higher Quality Content
- 60% Fewer Hallucinations
Browse by: Latest US Patents, China's latest patents, Technical Efficacy Thesaurus, Application Domain, Technology Topic, Popular Technical Reports.
© 2025 PatSnap. All rights reserved.Legal|Privacy policy|Modern Slavery Act Transparency Statement|Sitemap|About US| Contact US: help@patsnap.com