Long fiber reinforced nylon plastic and preparation method thereof
A nylon plastic, long fiber technology, applied in the field of plastic materials, can solve the problems of reduced impact resistance and flexural strength, reduced material shrinkage, affecting compatibility, etc., and achieves good molding conditions, good tensile strength, and good stability. Effects of sex and weather resistance
- Summary
- Abstract
- Description
- Claims
- Application Information
AI Technical Summary
Problems solved by technology
Method used
Image
Examples
Embodiment 1
[0021] (1) Take by weighing 88kgPA6, 12kg of alkali-free glass fibers with a diameter of 8 μm, 5kg of polyethylene glycol with an average molecular mass of 8000, 4kg of oleic acid, 3kg of maleic anhydride grafted polypropylene, 2-hydroxyl-4-n-octyl Oxybenzophenone 2kg, ethylene bis stearamide 1.5kg and phenyl phosphate diglycidyl ester 1kg;
[0022] (2) Add the above components into the high mixer in turn, the mixing temperature is controlled at 40°C, the mixing time is stopped after 3 minutes, and then the mixed materials are added to the hopper of the extruder, and the temperature is 240°C Melt extrusion under low temperature, cooling at 200°C, 160°C and 110°C in sequence, and pelletizing to obtain long fiber reinforced nylon plastic.
[0023] The performance test results of the prepared long fiber reinforced nylon plastic are shown in Table 1.
Embodiment 2
[0025] (1) Take by weighing 88kgPA6, 12kg of alkali-free glass fibers with a diameter of 8 μm, 8kg of polyethylene glycol with an average molecular mass of 8000, 4kg of oleic acid, 5kg of maleic anhydride grafted polypropylene, 2-hydroxyl-4-n-octyl Oxybenzophenone 2kg, ethylene bis stearamide 1.5kg and phenyl phosphate diglycidyl ester 1kg;
[0026] (2) Add the above components into the high mixer in turn, the mixing temperature is controlled at 40°C, the mixing time is stopped after 3 minutes, and then the mixed materials are added to the hopper of the extruder, and the temperature is 240°C Melt extrusion under low temperature, cooling at 200°C, 160°C and 110°C in sequence, and pelletizing to obtain long fiber reinforced nylon plastic.
[0027] The performance test results of the prepared long fiber reinforced nylon plastic are shown in Table 1.
Embodiment 3
[0029] (1) Weigh 96kgPA6, 15kg of alkali-free glass fiber with a diameter of 11 μm, 5kg of polyethylene glycol with an average molecular mass of 10,000, 6kg of oleic acid, 5kg of maleic anhydride grafted polypropylene, 2-hydroxyl-4-n-octyl Oxygen benzophenone 3kg, ethylene bis stearamide 3kg and phenyl phosphate diglycidyl ester 2kg;
[0030] (2) Add the above components into the high mixer in turn, the mixing temperature is controlled at 50°C, and the mixing time is stopped after 4 minutes, and then the mixed materials are added to the hopper of the extruder, and the temperature is 258°C Melt extrusion under low temperature, cooling at 200°C, 160°C and 110°C in sequence, and pelletizing to obtain long fiber reinforced nylon plastic.
[0031] The performance test results of the prepared long fiber reinforced nylon plastic are shown in Table 1.
PUM
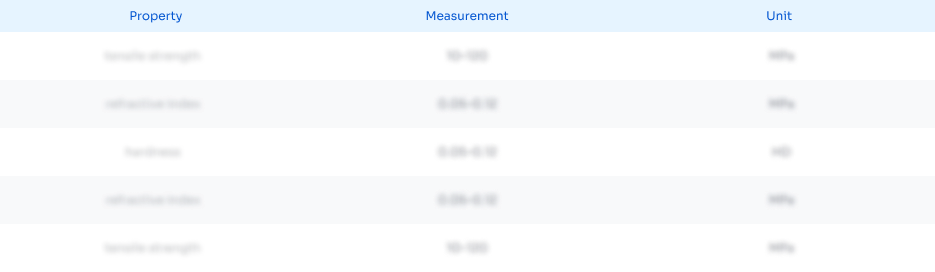
Abstract
Description
Claims
Application Information

- Generate Ideas
- Intellectual Property
- Life Sciences
- Materials
- Tech Scout
- Unparalleled Data Quality
- Higher Quality Content
- 60% Fewer Hallucinations
Browse by: Latest US Patents, China's latest patents, Technical Efficacy Thesaurus, Application Domain, Technology Topic, Popular Technical Reports.
© 2025 PatSnap. All rights reserved.Legal|Privacy policy|Modern Slavery Act Transparency Statement|Sitemap|About US| Contact US: help@patsnap.com