A kind of preparation method of zinc-aluminum alloy welding wire
A zinc-aluminum alloy, welding wire technology, applied in welding equipment, metal processing equipment, welding medium, etc., can solve the problems of unsatisfactory plastic processing performance and mechanical performance of welding wire, unsatisfactory performance of tube blank, uneven flux filling, etc. Achieve the effect of good solder mechanical properties, good surface finish, and automatic control
- Summary
- Abstract
- Description
- Claims
- Application Information
AI Technical Summary
Problems solved by technology
Method used
Image
Examples
Embodiment 1
[0027] Take the weight percentage as Al: 10%, and the balance as Zn, and do the batching. And take the ingredients as an example to illustrate the preparation process of the zinc aluminum alloy welding wire.
[0028] (1) Melting: Put the aluminum ingot into the melting furnace first, and then add the zinc ingot after melting, and after the melting is complete, pour the zinc-aluminum alloy solution into the casting holding furnace;
[0029] (2) Horizontal continuous casting: Pour the molten zinc-aluminum alloy solution into the casting holding furnace, and control the liquid level in the furnace so that the liquid level and the center line of the discharge hole form a certain height difference of 200 mm to maintain the zinc-aluminum alloy in the furnace The liquid temperature is 420℃, and the required drawing speed is 800mm / min to obtain the zinc-aluminum alloy rod blank.
[0030] (3) Cleaning: send the zinc-aluminum alloy rod blanks produced by the horizontal continuous casting proc...
Embodiment 2
[0035] Take the weight percentages as Al: 23%, Cu: 5%, and the balance as Zn, and carry out ingredients. And take the ingredients as an example to illustrate the preparation process of the zinc aluminum alloy welding wire.
[0036] (1) Melting: Put aluminum ingots into the smelting furnace first, and then add small copper lumps after melting, and finally add zinc ingots. After melting is complete, pour the zinc-aluminum alloy solution into the casting holding furnace;
[0037] (2) Horizontal continuous casting: Pour the molten zinc-aluminum alloy solution into the casting holding furnace, and control the liquid level in the furnace so that the liquid level and the center line of the discharge hole form a certain height difference of 50 mm to maintain the zinc-aluminum alloy in the furnace The liquid temperature is 550℃, and the required drawing speed is 50 mm / min to obtain the zinc-aluminum alloy rod.
[0038] (3) Cleaning: send the zinc-aluminum alloy rod blanks produced by the hor...
Embodiment 3
[0043] Take the weight percentages as Al: 11%, Cu: 2%, and the balance is Zn, and then mix. And take the ingredients as an example to illustrate the preparation process of the zinc aluminum alloy welding wire.
[0044] (1) Melting: Put aluminum ingots into the smelting furnace first, and then add small copper lumps after melting, and finally add zinc ingots. After melting is complete, pour the zinc-aluminum alloy solution into the casting holding furnace;
[0045] (2) Horizontal continuous casting: Pour the molten zinc-aluminum alloy solution into the casting holding furnace, and control the liquid level in the furnace so that the liquid level and the center line of the discharge hole form a certain height difference of 100 mm to maintain the zinc-aluminum alloy in the furnace The liquid temperature is 450℃, and the required drawing speed is 300 mm / min to obtain the zinc-aluminum alloy rod.
[0046] (3) Cleaning: send the zinc-aluminum alloy rod blanks produced by the horizontal con...
PUM
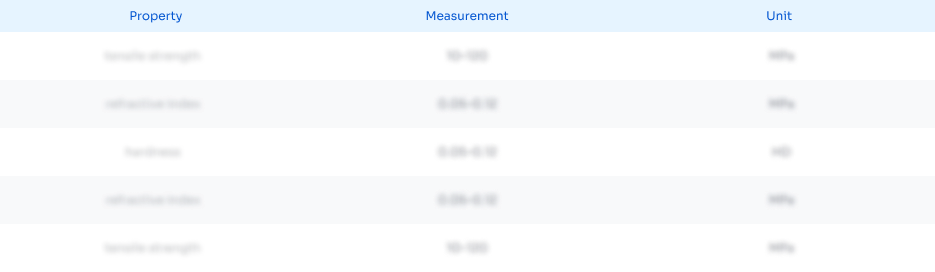
Abstract
Description
Claims
Application Information

- R&D Engineer
- R&D Manager
- IP Professional
- Industry Leading Data Capabilities
- Powerful AI technology
- Patent DNA Extraction
Browse by: Latest US Patents, China's latest patents, Technical Efficacy Thesaurus, Application Domain, Technology Topic, Popular Technical Reports.
© 2024 PatSnap. All rights reserved.Legal|Privacy policy|Modern Slavery Act Transparency Statement|Sitemap|About US| Contact US: help@patsnap.com