Polyurethane anticorrosive thermal-insulation paint and preparation method thereof
A technology of thermal insulation and polyurethane, applied in antifouling/underwater coatings, reflection/signal coatings, coatings, etc., can solve the problem of single function, achieve the effect of less consumption, good process performance, and reduced flow
- Summary
- Abstract
- Description
- Claims
- Application Information
AI Technical Summary
Problems solved by technology
Method used
Examples
Embodiment 1
[0049] First, in parts by weight, 45 parts of polyurethane prepolymer, 2 parts of diacetone acrylamide, 2 parts of dipropylene glycol dibenzoate, 0.7 part of aluminate coupling agent LS-822; 0.3 part of dispersant triethanolamine, rutile Type titanium dioxide 13 parts, defoamer OP-10 0.3 parts, kaolin 6 parts; mixed solvent (lignin + propylene glycol methyl ether + water, the weight ratio is 3:1:10) 11 parts, expanded perlite 5 parts, anticorrosion 3 parts of agent (Nordes C15 bactericidal preservative); 2 parts of leveling agent cellulose acetate butyrate, 2 parts of iron oxide yellow, for material preparation.
[0050] The production method is to add 2.4 kg of ethanol with a volume concentration of 55-85% per kg of diacetone acrylamide to dissolve, and then mix it with polyurethane prepolymer in a reaction kettle. The reaction temperature is 80°C, and the reaction time is 2 hours. Ester coupling agent LS-822 and dispersant triethanolamine; continue to react for 5 hours; then...
Embodiment 2
[0052] First, in parts by weight, 50 parts of polyurethane prepolymer, 3 parts of diacetone acrylamide, 3 parts of dipropylene glycol dibenzoate, 0.9 part of aluminate coupling agent LS-822; 0.5 part of dispersant triethanolamine, rutile Type titanium dioxide 15 parts, defoamer
[0053] 0.4 parts of OP—10, 8 parts of kaolin; 13 parts of mixed solvent (lignin + propylene glycol methyl ether + water, the weight ratio is 3:1:10), 7 parts of expanded perlite, preservative (1,2-benzoiso Thiazolin-3-one) 5 parts; antifreeze agent glycerol 4 parts, iron oxide red 1 part, for material preparation.
[0054] The production method is to add 2.4 kg of ethanol with a volume concentration of 55-85% per kg of diacetone acrylamide to dissolve, and then mix it with polyurethane prepolymer in a reaction kettle. The reaction temperature is 120°C, and the reaction time is 1 hour. Add alumina acid Ester coupling agent LS-822 and dispersant triethanolamine; continue to react for 4 hours; then add ...
Embodiment 3
[0056] First, in parts by weight, 55 parts of polyurethane prepolymer, 4 parts of diacetone acrylamide, 5 parts of dipropylene glycol dibenzoate, 1 part of aluminate coupling agent LS-822; 0.6 part of dispersant triethanolamine, rutile Type titanium dioxide 18 parts, defoamer OP-10 0.5 parts, kaolin 10 parts; mixed solvent (lignin + propylene glycol methyl ether + water, the weight ratio is 3:1:10) 15 parts, expanded perlite 9 parts, anticorrosion agent (1,2-benzisothiazolin-3-one) 7 parts; anti-sedimentation agent organobentonite 6 parts, for material preparation.
[0057] The production method is to add 2.4 kilograms of ethanol with a volume concentration of 55-85% per kilogram of diacetone acrylamide to dissolve, and then mix it with polyurethane prepolymer in a reaction kettle. The reaction temperature is 140 ° C, and the reaction time is 1.5 hours. Ester coupling agent LS-822 and dispersant triethanolamine; continue to react for 3 hours; then add dipropylene glycol dibenz...
PUM
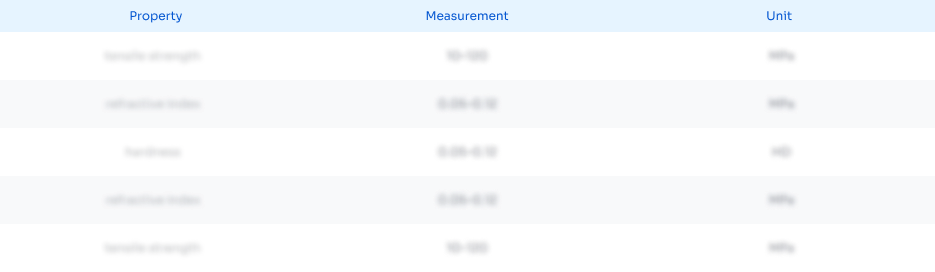
Abstract
Description
Claims
Application Information

- Generate Ideas
- Intellectual Property
- Life Sciences
- Materials
- Tech Scout
- Unparalleled Data Quality
- Higher Quality Content
- 60% Fewer Hallucinations
Browse by: Latest US Patents, China's latest patents, Technical Efficacy Thesaurus, Application Domain, Technology Topic, Popular Technical Reports.
© 2025 PatSnap. All rights reserved.Legal|Privacy policy|Modern Slavery Act Transparency Statement|Sitemap|About US| Contact US: help@patsnap.com