Rotary die-cutting die roller directly formed by laser cladding
A technology of rotating molds and mold rollers, which is applied in metal material coating process, metal processing, coating, etc. It can solve the problems such as the great difference between the wall thickness of the model and the thickness of the substrate, difficulty in maintaining accuracy, and coarse grains in the internal structure. , to achieve the moment of inertia of the good mold roller, reduce the need for subsequent processing, and control the cost
- Summary
- Abstract
- Description
- Claims
- Application Information
AI Technical Summary
Problems solved by technology
Method used
Image
Examples
Embodiment Construction
[0027] see figure 1 and figure 2 As shown, a mold roll of a rotary die-cutting equipment includes a roll body 1 on which a blade 2 is provided, and the roll body 1 adopts a laser cladding process to form a cladding layer 11 from the outside to the inside. 1. The layered structure of the transition layer 12 and the matrix 13, the cladding layer 11 constitutes the blade 2, and the transition layer connects the blade 2 and the matrix 13; the roller body is a hollow structure.
[0028] The laser cladding process realizes the metallurgical bonding between the substrate and the cladding layer through the deposition of metal alloys or other types of materials on the substrate, and obtains a non-porous, fine-grained microstructure, and cladding with good mechanical properties Floor. Compared with laser sintering and coating processes such as plasma spraying and high-speed flame spraying, the bonding and friction properties of the cladding layer are better; compared with other metal...
PUM
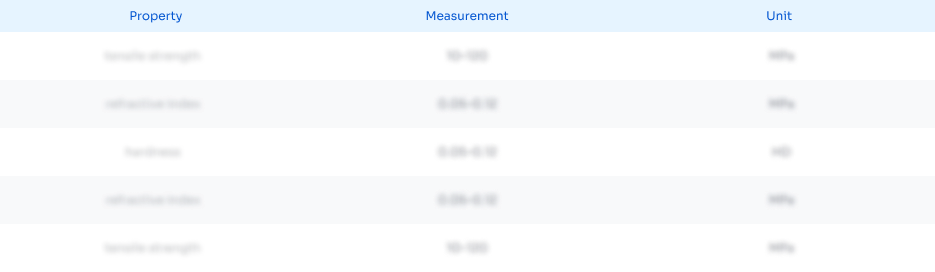
Abstract
Description
Claims
Application Information

- R&D Engineer
- R&D Manager
- IP Professional
- Industry Leading Data Capabilities
- Powerful AI technology
- Patent DNA Extraction
Browse by: Latest US Patents, China's latest patents, Technical Efficacy Thesaurus, Application Domain, Technology Topic, Popular Technical Reports.
© 2024 PatSnap. All rights reserved.Legal|Privacy policy|Modern Slavery Act Transparency Statement|Sitemap|About US| Contact US: help@patsnap.com