Method for removing nitride from heavy oil
A nitride and removal technology, applied in the petroleum industry, processing hydrocarbon oil, refining hydrocarbon oil, etc., can solve the problems of high viscosity, complex composition, high processing cost, and achieve good technical effect.
- Summary
- Abstract
- Description
- Claims
- Application Information
AI Technical Summary
Problems solved by technology
Method used
Image
Examples
preparation example 1
[0070] Preparation Example 1: Preparation of Denitrification Agent T1
[0071] S1: N, N, N-triethylammonium bromide ([(C 2 h 5 ) 3 NH]Br, also known as triethylamine hydrobromide or triethylamine hydrobromide) and aluminum trichloride (AlCl 3 ) were mixed according to a molar ratio of 1:1, stirred and mixed at room temperature for 20 minutes, then raised to 80°C, and kept stirring at this temperature for 2 hours. After the reaction was completed, naturally cooled to room temperature and dried to obtain the basic ion liquid;
[0072] S2: gac is added into the hydrochloric acid aqueous solution that molar concentration is 1mol / L (the mass volume ratio of gac and hydrochloric acid aqueous solution is 1:5g / ml), reflux treatment 2 hours, then filter to obtain solid A; In mixed acid (a mixture of concentrated sulfuric acid and concentrated nitric acid with a volume ratio of 2:1) was stirred for 20 minutes (the mass volume ratio of the solid A to the mixed acid was 1:8 g / ml), fil...
preparation example 2
[0075] Preparation Example 2: Preparation of Denitrification Agent T2
[0076] S1: N,N-diisopropylammonium chloride ([(i-Pr) 2 NH 2 ]Cl, also known as diisopropylamine hydrochloride or diisopropylamine hydrochloride) and ferric chloride (FeCl 3 ) were mixed according to a molar ratio of 1:2, stirred and mixed at room temperature for 30 minutes, then raised to 90°C, and kept stirring at this temperature for 4 hours. After the reaction was completed, naturally cooled to room temperature and dried to obtain the basic ion liquid;
[0077] S2: SiO 2 Added to the aqueous solution of nitric acid with a molar concentration of 2mol / L (SiO 2 The mass volume ratio with the nitric acid aqueous solution is 1:15g / ml), reflux treatment for 6 hours, and then filter to obtain solid A; Solid A is again mixed in a mixed acid (volume ratio is 3:1 The mixing of concentrated sulfuric acid and concentrated nitric acid solution) with stirring for 35 minutes (the mass volume ratio of the solid A ...
preparation example 3
[0080] Preparation Example 3: Preparation of Denitrification Agent T3
[0081] S1: N-benzyl-N-isopropylammonium chloride ([(i-Pr)(C 6 h 5 CH 2 )NH 2 ]Cl, also known as N-benzylisopropylamine hydrochloride or N-benzylisopropylamine hydrochloride) and aluminum tribromide (AlBr 3 ) were mixed at a molar ratio of 1:3, stirred and mixed at room temperature for 40 minutes, then raised to 100°C, and kept stirring at this temperature for 2 hours. After the reaction was completed, naturally cooled to room temperature and dried to obtain the basic ion liquid;
[0082] S2: Aluminum oxide is added to the aqueous sulfuric acid solution whose molar concentration is 3mol / L (the mass volume ratio of aluminum oxide and sulfuric acid aqueous solution is 1:25g / ml), reflux treatment for 10 hours, and then filter to obtain solid A; A was stirred again in the mixed acid (a mixture of concentrated sulfuric acid and concentrated nitric acid with a volume ratio of 4:1) for 50 minutes (the mass vo...
PUM
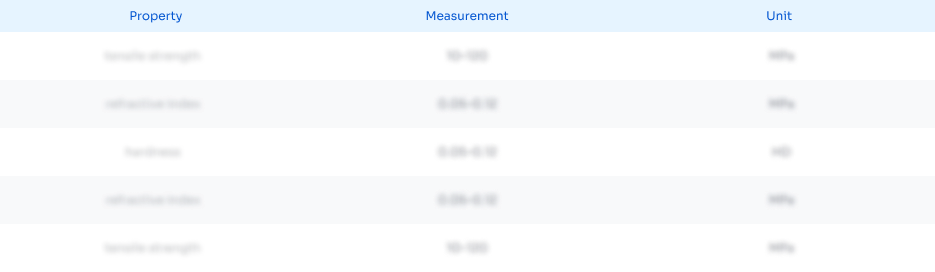
Abstract
Description
Claims
Application Information

- Generate Ideas
- Intellectual Property
- Life Sciences
- Materials
- Tech Scout
- Unparalleled Data Quality
- Higher Quality Content
- 60% Fewer Hallucinations
Browse by: Latest US Patents, China's latest patents, Technical Efficacy Thesaurus, Application Domain, Technology Topic, Popular Technical Reports.
© 2025 PatSnap. All rights reserved.Legal|Privacy policy|Modern Slavery Act Transparency Statement|Sitemap|About US| Contact US: help@patsnap.com