Chemical oxidation liquid for magnesium alloy
A chemical oxidation and magnesium alloy technology, applied in the field of chemical oxidation solution, can solve the problems of high content of hexavalent chromium ions, poor corrosion resistance of oxide film, low production efficiency, etc., to reduce environmental pollution and production costs, strong adhesion, The effect of short passivation time
- Summary
- Abstract
- Description
- Claims
- Application Information
AI Technical Summary
Problems solved by technology
Method used
Examples
Embodiment 1
[0014] Add 3.5g of potassium dichromate, 0.95g of potassium aluminum sulfate, 0.12g of ammonium fluoride, and 0.6g of acetic acid into 100g of water, stir and dissolve evenly to obtain solution A. Take 0.6g of citric acid, 0.12g of boric acid, and 0.12g of mixed rare earths and add them into 100g of water, stir and dissolve to obtain solution B evenly. Mix solution A and solution B, add water to 1kg, stir and mix evenly to obtain a chemical oxidation solution.
[0015] Keep the pH value of the chemical oxidation solution at 2.0 and the temperature at 45°C, immerse the degreased and pickled magnesium alloy test piece in the chemical oxidation solution for passivation for 180s, take it out for washing, and dry at 60°C to obtain iridescent Passivation film layer sample 1. Keeping other process conditions unchanged, the passivation time was shortened to 150s, and a similar iridescent oxide film sample 2 was obtained. The above two samples were subjected to a neutral salt spray t...
Embodiment 2
[0017] Add 5 g of potassium dichromate, 1.3 g of potassium aluminum sulfate, 0.18 g of ammonium fluoride, and 0.85 g of acetic acid into 100 g of water, stir and dissolve evenly to obtain solution A. Take 0.9g of citric acid, 0.18g of boric acid, and 0.18g of mixed rare earths and add them into 100g of water, stir and dissolve to obtain solution B evenly. Mix solution A and solution B, add water to 1kg, stir and mix evenly to obtain a chemical oxidation solution.
[0018] Keep the pH value of the chemical oxidation solution at 2.0 and the temperature at 45°C, immerse the degreased and pickled magnesium alloy test piece in the chemical oxidation solution for passivation for 180s, take it out for washing, and dry at 60°C to obtain iridescent Passivation film layer sample 3. Keeping other process conditions unchanged, the passivation time was shortened to 150s, and a similar iridescent oxide film sample 4 was obtained. The above two samples were subjected to neutral salt spray ...
Embodiment 3
[0020] Add 6.5g of potassium dichromate, 1.65g of potassium aluminum sulfate, 0.24g of ammonium fluoride, and 1g of acetic acid into 100g of water, stir and dissolve evenly to obtain solution A. Take 1.2g of citric acid, 0.24g of boric acid, and 0.24g of mixed rare earths and add them into 100g of water, stir and dissolve to obtain solution B evenly. Mix solution A and solution B, add water to 1kg, stir and mix evenly to obtain a chemical oxidation solution.
[0021] Keep the pH value of the chemical oxidation solution at 2.3 and the temperature at 45°C, immerse the degreased and pickled magnesium alloy test piece in the chemical oxidation solution for passivation for 180s, take it out and wash it, and dry it at 60°C to obtain iridescent Passivation film layer sample 5. Keeping other process conditions unchanged, the passivation time was shortened to 150s, and a similar iridescent oxide film sample 6 was obtained. The above two samples were subjected to neutral salt spray te...
PUM
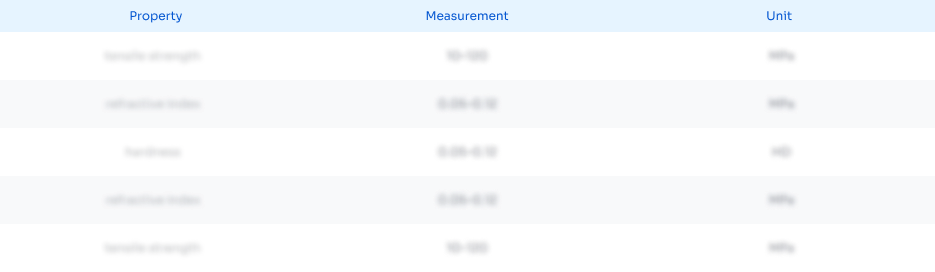
Abstract
Description
Claims
Application Information

- R&D
- Intellectual Property
- Life Sciences
- Materials
- Tech Scout
- Unparalleled Data Quality
- Higher Quality Content
- 60% Fewer Hallucinations
Browse by: Latest US Patents, China's latest patents, Technical Efficacy Thesaurus, Application Domain, Technology Topic, Popular Technical Reports.
© 2025 PatSnap. All rights reserved.Legal|Privacy policy|Modern Slavery Act Transparency Statement|Sitemap|About US| Contact US: help@patsnap.com