Deslagging method for continuous production of methyl isocyanate
A technology of methyl isocyanate and polymethyl isocyanate, which is applied in the field of slag removal in the continuous production of methyl isocyanate, can solve the problems of high production cost, high labor intensity, environmental pollution, etc., and reduce equipment occupation and basic investment costs , reduce the labor intensity of employees, and improve the effect of solvent reuse rate
- Summary
- Abstract
- Description
- Claims
- Application Information
AI Technical Summary
Problems solved by technology
Method used
Image
Examples
Embodiment 1
[0026] Composition of the liquid phase outlet material from the vapor-liquid separator: methylcarbamoyl chloride 165.71kg / hr, methyl isocyanate 15.12kg / hr, solvent chloroform 1539.48kg / hr, trimeric methyl isocyanate solid slag 2.90kg / hr. The liquid phase outlet material continuously enters the slag remover from the feed port 4 of the slag remover, and is continuously filtered under negative pressure. When the pressure of the filter cake is 0.09MPa, switch the incoming material to the standby slag remover, lower the stirring system 1 of the slag remover and start stirring, start the heating jacket 5, the stirring speed is 20rpm, and the superheated steam temperature is 150°C. Stir and heat to evaporate and remove volatile components such as methyl carbamoyl chloride, methyl isocyanate and solvent contained in the filter cake, and the steam is connected to the condenser through the steam outlet 2 to condense; after the filter cake is evaporated to dryness, stop the heating jacket...
Embodiment 2
[0028] Composition of the liquid phase outlet material from the vapor-liquid separator: methylcarbamoyl chloride 165.71kg / hr, methyl isocyanate 15.12kg / hr, solvent chloroform 1539.48kg / hr, trimeric methyl isocyanate solid slag 2.90kg / hr. The mixed material continuously enters the slag remover from the feed port 4, and is continuously filtered under negative pressure. When the pressure of the filter cake is 0.08MPa, switch the incoming material to the standby slag remover, lower the stirring system 1 of the slag remover and start stirring, start the heating jacket 5, the stirring speed is 15rpm, and the superheated steam temperature is 130°C. Stir and heat to evaporate and remove volatile components such as methyl carbamoyl chloride, methyl isocyanate and solvent contained in the filter cake, and the steam is connected to the condenser through the steam outlet 2 to condense; after the filter cake is evaporated to dryness, stop the heating jacket 5, Switch the stirring system 1 ...
Embodiment 3
[0030] Composition of the liquid phase outlet material from the vapor-liquid separator: methylcarbamoyl chloride 165.71kg / hr, methyl isocyanate 15.12kg / hr, solvent chloroform 1539.48kg / hr, trimeric methyl isocyanate solid slag 2.90kg / hr. The mixed material continuously enters the slag remover from the feed port, and is fed with nitrogen and filtered under pressure. When the pressure of the filter cake drops to 0.085MPa, switch the incoming material to the standby slag remover, lower the agitator that comes with the slag remover, start the stirring in the system 1, start the heating jacket 5, the stirring speed is 10rpm, and the superheated steam temperature is 140 ℃, stirring and heating to evaporate to remove volatile components such as methylcarbamoyl chloride, methyl isocyanate and solvent contained in the filter cake, and the steam is connected to the condenser through steam outlet 2 for condensation; after the filter cake is evaporated to dryness, stop the heating jacket ...
PUM
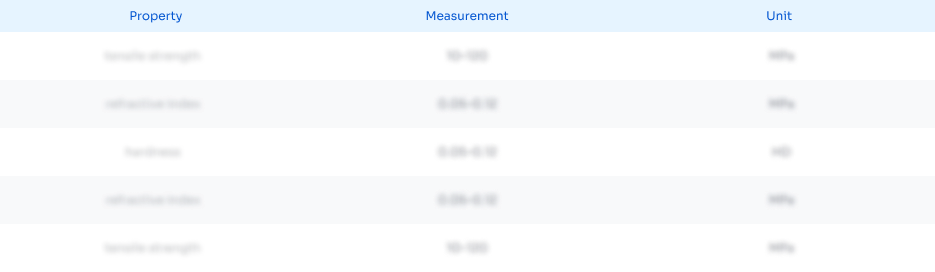
Abstract
Description
Claims
Application Information

- R&D
- Intellectual Property
- Life Sciences
- Materials
- Tech Scout
- Unparalleled Data Quality
- Higher Quality Content
- 60% Fewer Hallucinations
Browse by: Latest US Patents, China's latest patents, Technical Efficacy Thesaurus, Application Domain, Technology Topic, Popular Technical Reports.
© 2025 PatSnap. All rights reserved.Legal|Privacy policy|Modern Slavery Act Transparency Statement|Sitemap|About US| Contact US: help@patsnap.com