A method for preparing solar single crystal back-polished cells
A technology of back polishing and solar energy, applied in photovoltaic power generation, circuits, electrical components, etc., can solve problems such as high cost, environmental pollution, and increased production costs, and achieve the goals of reducing production costs, improving uniformity of square resistance, and increasing the lifetime of minority carriers Effect
- Summary
- Abstract
- Description
- Claims
- Application Information
AI Technical Summary
Problems solved by technology
Method used
Examples
Embodiment 1
[0027] (a) After texturizing and diffusing 50 pieces of 156-type monocrystalline silicon wafers, use HF and HNO in the wet etching bath 3 Solution etching to remove the PSG and PN junctions on the back;
[0028] (b) Immerse in a 160g / L sodium hydroxide solution with 7mL / L absolute ethanol at a temperature of 65°C, and ultrasonically polish for 120s by bubbling;
[0029] (c) pickling, washing and drying the single crystal silicon wafer after back polishing with HF;
[0030] (d) Using PECVD to deposit silicon nitride on the front side of the single crystal silicon wafer, and perform electrode printing and sintering to complete the production of the entire battery.
[0031] Among them, the reflectance of the back surface of the silicon wafer after back polishing is tested, the reflectance of the front surface of the silicon wafer after pickling and water washing is tested, and the electrical performance of the finished battery is tested.
Embodiment 2
[0033] (a) After texturizing and diffusing 50 pieces of 156-type monocrystalline silicon wafers, use HF and HNO in the wet etching bath 3 Solution etching to remove the PSG and PN junctions on the back;
[0034] (b) Immerse in a 120g / L sodium hydroxide solution with 7mL / L absolute ethanol at a temperature of 75°C, and ultrasonically polish for 180s by bubbling;
[0035] (c) pickling, washing and drying the single crystal silicon wafer after back polishing with HF;
[0036] (d) Using PECVD to deposit silicon nitride on the front side of the single crystal silicon wafer, and perform electrode printing and sintering to complete the production of the entire battery.
[0037] Among them, the reflectance of the back surface of the silicon wafer after back polishing is tested, the reflectance of the front surface of the silicon wafer after pickling and water washing is tested, and the electrical performance of the finished battery is tested.
Embodiment 3
[0039] (a) After texturizing and diffusing 50 pieces of 156-type monocrystalline silicon wafers, use HF and HNO in the wet etching bath 3 Solution etching to remove the PSG and PN junctions on the back;
[0040] (b) Immerse in a 100g / L sodium hydroxide solution with 7mL / L absolute ethanol at a temperature of 60°C, and bubble and ultrasonically polish for 600s;
[0041] (c) pickling, washing and drying the single crystal silicon wafer after back polishing with HF;
[0042] (d) Using PECVD to deposit silicon nitride on the front side of the single crystal silicon wafer, and perform electrode printing and sintering to complete the production of the entire battery.
[0043] Among them, the reflectance of the back surface of the silicon wafer after back polishing is tested, the reflectance of the front surface of the silicon wafer after pickling and water washing is tested, and the electrical performance of the finished battery is tested.
PUM
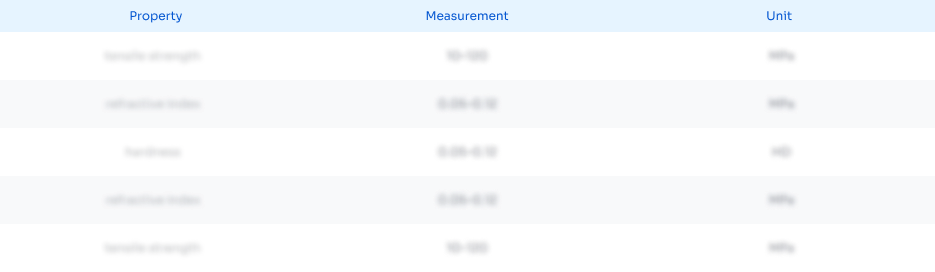
Abstract
Description
Claims
Application Information

- Generate Ideas
- Intellectual Property
- Life Sciences
- Materials
- Tech Scout
- Unparalleled Data Quality
- Higher Quality Content
- 60% Fewer Hallucinations
Browse by: Latest US Patents, China's latest patents, Technical Efficacy Thesaurus, Application Domain, Technology Topic, Popular Technical Reports.
© 2025 PatSnap. All rights reserved.Legal|Privacy policy|Modern Slavery Act Transparency Statement|Sitemap|About US| Contact US: help@patsnap.com