Silicon-aluminum alloy and preparation method thereof
A technology of silicon-aluminum alloy and aluminum alloy, which is applied in the field of silicon-aluminum alloy and its preparation, can solve the problems of unreasonable aluminum alloy components, poor processing methods, and easy fracture, etc., and achieve high quality, consistent grain size, Good wear resistance
- Summary
- Abstract
- Description
- Claims
- Application Information
AI Technical Summary
Problems solved by technology
Method used
Examples
Embodiment 1
[0018] A silicon-aluminum alloy, containing the following components in weight percentage: 6% magnesium, 8% silicon, 0.05% iron, 0.05% copper, 0.02% manganese, 0.06% chromium, 0.08% nickel, 0.1% zinc, bismuth 0.02%, titanium 0.1%, and the rest is aluminum.
[0019] The manufacture method of described silicon-aluminum alloy is:
[0020] (1) Put aluminum, magnesium and silicon into the smelting furnace, heat it to 800°C in an environment filled with nitrogen to melt it into a melt, then add iron and copper to the melt with a gas carrier, and keep stirring at a constant temperature 8min, then adjust the temperature to 780°C, blow argon in the smelting furnace to refine the mixed melt for 15min, and remove the scum on the liquid surface to obtain a mixed melt;
[0021] (2) Send the mixed melt into the intermediate frequency furnace, raise the temperature to 1150°C, add manganese, chromium, nickel, titanium, zinc and bismuth, and keep it for 12 minutes, then send the material into...
Embodiment 2
[0023] A silicon-aluminum alloy, containing the following components in weight percent: 7% magnesium, 10% silicon, 0.08% iron, 0.09% copper, 0.06% manganese, 0.1% chromium, 0.1% nickel, 0.1% zinc, bismuth 0.02%, titanium 0.1%, and the rest is aluminum.
[0024] The manufacture method of described silicon-aluminum alloy is:
[0025] (1) Put aluminum, magnesium and silicon into the smelting furnace, heat it to 800°C in an environment filled with nitrogen to melt it into a melt, then add iron and copper to the melt with a gas carrier, and keep stirring at a constant temperature 4min, then adjust the temperature to 780°C, blow argon in the smelting furnace to refine the mixed melt for 16min, and remove the scum on the liquid surface to obtain a mixed melt;
[0026] (2) Send the mixed melt into the intermediate frequency furnace, raise the temperature to 1250°C, add manganese, chromium, nickel, titanium, zinc and bismuth, keep it for 12 minutes, then send the material into the inj...
Embodiment 3
[0028] A silicon-aluminum alloy, containing the following components in weight percentage: 10% magnesium, 16% silicon, 0.15% iron, 0.2% copper, 0.15% manganese, 0.25% chromium, 0.22% nickel, 0.5% zinc, bismuth 0.1%, titanium 0.2%, and the rest is aluminum.
[0029] The manufacture method of described silicon-aluminum alloy is:
[0030] (1) Put aluminum, magnesium and silicon into the smelting furnace, heat it to 805°C in an environment filled with nitrogen to melt it into a melt, then add iron and copper to the melt with a gas carrier, and keep stirring at a constant temperature 5min, then adjust the temperature to 780°C, blow argon in the smelting furnace to refine the mixed melt for 15min, and remove the scum on the liquid surface to obtain a mixed melt;
[0031] (2) Send the mixed melt into the intermediate frequency furnace, raise the temperature to 1200°C, add manganese, chromium, nickel, titanium, zinc and bismuth, keep it for 9 minutes, and then send the material into ...
PUM
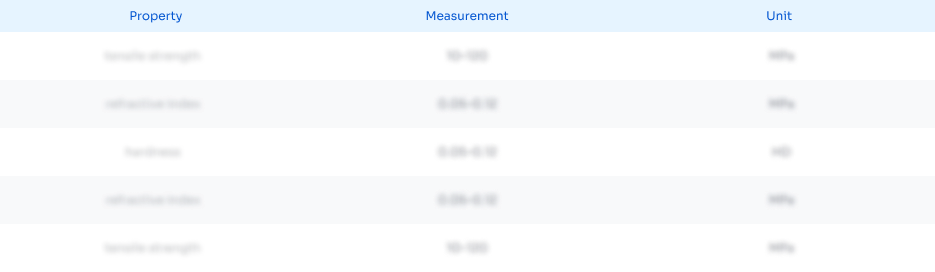
Abstract
Description
Claims
Application Information

- R&D
- Intellectual Property
- Life Sciences
- Materials
- Tech Scout
- Unparalleled Data Quality
- Higher Quality Content
- 60% Fewer Hallucinations
Browse by: Latest US Patents, China's latest patents, Technical Efficacy Thesaurus, Application Domain, Technology Topic, Popular Technical Reports.
© 2025 PatSnap. All rights reserved.Legal|Privacy policy|Modern Slavery Act Transparency Statement|Sitemap|About US| Contact US: help@patsnap.com