Coal ash composite floor
A composite floor and fly ash technology, applied in the field of flooring, can solve the problems of flame retardancy, weak anti-static and anti-aging properties, excessive formaldehyde content, and reduced service life, etc., and achieves easy air circulation, hard texture, and increased stability. Effect
- Summary
- Abstract
- Description
- Claims
- Application Information
AI Technical Summary
Problems solved by technology
Method used
Image
Examples
Embodiment 1
[0018] The raw material formula ratio of a kind of fly ash composite floor is:
[0019] 280 mesh fly ash 131kg, 80 mesh fly ash 9kg, 1mm rock wool 0.06kg, PVC 46kg, 1100 mesh talc powder 14kg, lead salt composite stabilizer 1.5kg, AC foaming agent 0.11kg, CPE (chlorinated polyethylene ) 1.9kg, ACR401 0.7kg, PE wax 1.5kg.
[0020] A kind of preparation method of fly ash composite floor is:
[0021] (1) Weigh the materials according to the ratio of the above raw material formula;
[0022] (2) Pour the above-mentioned weighed fly ash and talcum powder into a thermomixer and stir fully for 18 minutes, then add PVC and fully stir for 9 minutes, then add other materials in the above formula and fully stir to obtain a mixture;
[0023] (3) Put the above compound into the storage hopper of the extruder, and control the feeding amount of the compound by controlling the screw rotation number of the extruder;
[0024] (4) By controlling the feeding speed and screw speed of the extrude...
Embodiment 2
[0028] The raw material formula ratio of a kind of fly ash composite floor is:
[0029] 300 mesh fly ash 130kg, 100 mesh fly ash 8kg, 1mm rock wool 0.05kg, PVC 45kg, 1200 mesh talc powder 13kg, lead salt composite stabilizer 1.4kg, AC foaming agent 0.1kg, CPE (chlorinated polyethylene ) 1.8kg, ACR401 0.7kg, PE wax 1.5kg.
[0030] A kind of preparation method of fly ash composite floor is:
[0031] (1) Weigh the materials according to the ratio of the above raw material formula;
[0032] (2) Pour the above-mentioned weighed fly ash and talcum powder into a thermomixer and stir fully for 20 minutes, then add PVC and fully stir for 10 minutes, then add other materials in the above formula and fully stir to obtain a mixture;
[0033] (3) Put the above compound into the storage hopper of the extruder, and control the feeding amount of the compound by controlling the screw rotation number of the extruder;
[0034] (4) By controlling the feeding speed and screw speed of the extrud...
Embodiment 3
[0038] The raw material formula ratio of a kind of fly ash composite floor is:
[0039] 290 mesh fly ash 132kg, 90 mesh fly ash 10kg, 1mm rock wool 0.05kg, PVC 48kg, 1200 mesh talcum powder 15kg, lead salt composite stabilizer 1.5kg, AC foaming agent 0.12kg, CPE (chlorinated polyethylene ) 2kg, ACR401 0.8kg, PE wax 1.6kg.
[0040] A kind of preparation method of fly ash composite floor is:
[0041] (1) Weigh the materials according to the ratio of the above raw material formula;
[0042] (2) Pour the above-mentioned weighed fly ash and talcum powder into a thermomixer and stir fully for 22 minutes, then add PVC and fully stir for 11 minutes, then add other materials in the above formula and fully stir to obtain a mixture;
[0043] (3) Put the above compound into the storage hopper of the extruder, and control the feeding amount of the compound by controlling the screw rotation number of the extruder;
[0044] (4) By controlling the feeding speed and screw speed of the extru...
PUM
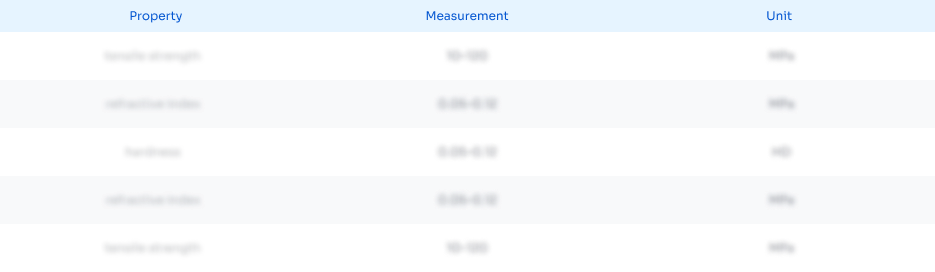
Abstract
Description
Claims
Application Information

- R&D Engineer
- R&D Manager
- IP Professional
- Industry Leading Data Capabilities
- Powerful AI technology
- Patent DNA Extraction
Browse by: Latest US Patents, China's latest patents, Technical Efficacy Thesaurus, Application Domain, Technology Topic, Popular Technical Reports.
© 2024 PatSnap. All rights reserved.Legal|Privacy policy|Modern Slavery Act Transparency Statement|Sitemap|About US| Contact US: help@patsnap.com