Tin-containing molecular sieve catalyst for hydration of ethylene oxide to prepare ethylene glycol and method of use
A technology for ethylene oxide and catalyst, which is applied to a tin-containing molecular sieve catalyst for preparing ethylene glycol by hydration of ethylene oxide and its application field, can solve the problems of high water ratio, environmental pollution, high energy consumption and the like, and achieves the preparation process. Simple, low-cost, selectivity-enhancing effect
- Summary
- Abstract
- Description
- Claims
- Application Information
AI Technical Summary
Problems solved by technology
Method used
Image
Examples
preparation example Construction
[0033] The preparation method of the catalyst that is used for the direct hydration of epoxy compound to prepare ethylene glycol provided by the invention comprises the following steps:
[0034] Step 1) SiO 2 / Al 2 o 3 The original powder of H-SSZ-13 molecular sieve with a value of 27 is first dealuminated under the condition of water vapor or concentrated nitric acid, concentrated hydrochloric acid or oxalic acid solution. The steam treatment conditions are as follows: 1-5g of H-SSZ-13 molecular sieve raw powder is placed in a tube furnace, and then treated with steam under high temperature conditions, the treatment temperature is 500-800°C, and the treatment time is 3- 10h; the acid treatment conditions are: put 5-10g of H-SSZ-13 molecular sieve raw powder in a 500ml round-bottomed three-necked flask, then add 100-200ml of concentrated nitric acid, concentrated hydrochloric acid or oxalic acid solution, under the condition of oil bath Perform stirring treatment, the treat...
Embodiment 1
[0044] The preparation process of the 2%Sn-SSZ-13 catalyst used in the present embodiment comprises the following steps:
[0045] 1) In this experiment, the H-SSZ-13 catalyst was used as the original powder, and the silicon-aluminum ratio of the catalyst (SiO 2 / A 2 o 3 ) is 27, and the grain size is 100-500nm. In addition, the XRD results show that the catalyst has a good CHA structure without the presence of heterocrystals (see figure 1 ). In the preparation process of Sn-SSZ-13, a certain amount of H-SSZ-13 raw powder is firstly weighed and treated under the condition of water vapor or concentrated acid. The steam treatment conditions are as follows: the raw H-SSZ-13 molecular sieve powder is placed in a tube furnace, and then treated with steam under high temperature conditions, the treatment temperature is 600 ° C, and the treatment time is 5 hours; the acid treatment conditions are: concentrated nitric acid , concentrated hydrochloric acid or oxalic acid solution ar...
Embodiment 2
[0057] Example 2: This example investigates the effect of different roasting methods, i.e. muffle furnace and vacuum tube furnace roasting at 550°C, on the hydration performance of 2% Sn-SSZ-13 catalyst, and other reaction conditions are the same as in the examples 1 described. The catalytic performance evaluation is shown in Table 2:
[0058] Table 2 The influence of the calcination mode of the catalyst on the process of preparing ethylene glycol by hydration of ethylene oxide
[0059]
[0060] The evaluation results of the catalyst show that the catalyst calcined in the vacuum tube furnace has better performance than the sample directly calcined in the muffle furnace. Depend on figure 2 and image 3 The ultraviolet results show that the tin species in the sample calcined in the vacuum tube furnace mainly exist in the form of four-coordinated tin at 215nm, while a large part of the sample calcined in the muffle furnace is the tin oxide species at 250nm. exist. Tin ox...
PUM
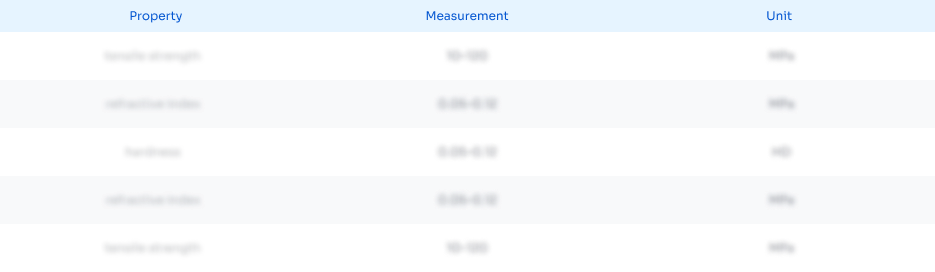
Abstract
Description
Claims
Application Information

- R&D
- Intellectual Property
- Life Sciences
- Materials
- Tech Scout
- Unparalleled Data Quality
- Higher Quality Content
- 60% Fewer Hallucinations
Browse by: Latest US Patents, China's latest patents, Technical Efficacy Thesaurus, Application Domain, Technology Topic, Popular Technical Reports.
© 2025 PatSnap. All rights reserved.Legal|Privacy policy|Modern Slavery Act Transparency Statement|Sitemap|About US| Contact US: help@patsnap.com