Automobile brake lining
A technology for automobile braking and brake lining, which is applied in the direction of brake parts, other chemical processes, chemical instruments and methods, etc., can solve the problem of high braking noise, poor wear resistance and heat dissipation performance of friction brake linings , unstable friction coefficient, etc., to achieve moderate hardness, good economic and social benefits, and avoid recession and expansion.
- Summary
- Abstract
- Description
- Claims
- Application Information
AI Technical Summary
Problems solved by technology
Method used
Examples
Embodiment 1
[0012] Embodiment 1: ceramic fiber 16.5%, carbon fiber 5%, cellulose fiber 3.5%, aramid fiber 13%, modified phenolic resin 9%, aluminum oxide 2%, barium sulfide 3%, graphite 6%, 5% of zircon, 12% of quartz sand, 1.5% of bauxite, 1.5% of zinc oxide, 3.5% of nitrile rubber, 1.5% of antimony sulfide, 8% of friction powder, and 9% of nano-silicon carbide are put into the high-speed disperser, Stir it into powder, take it out, put it into the forming mold, and press it into the mold, then put it into the flat vulcanizing machine at a high temperature of 270°C and a pressure of 20-23MPa, keep it for 20 minutes, then take out the brake pads and remove the burrs That is, it becomes a finished product.
Embodiment 2
[0013] Embodiment 2: ceramic fiber 18%, carbon fiber 4%, cellulose fiber 7%, aramid fiber 9%, modified phenolic resin 12%, aluminum oxide 3%, barium sulfide 4%, graphite 7%, Put 5% zircon, 10% quartz sand, 1% bauxite, 1% zinc oxide, 2% nitrile rubber, 2% antimony sulfide, 9% friction powder, and 6% nano-silicon carbide into the high-speed disperser, Stir it into powder, take it out, put it into the forming mold, and press it into the mold, then put it into the flat vulcanizing machine at a high temperature of 270°C and a pressure of 20-23MPa, keep it for 20 minutes, then take out the brake pads and remove the burrs That is, it becomes a finished product.
PUM
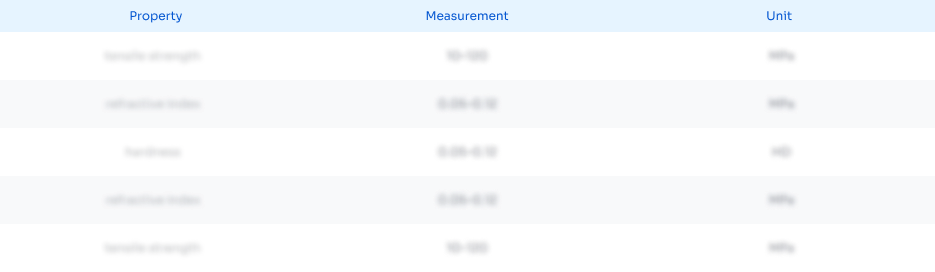
Abstract
Description
Claims
Application Information

- R&D
- Intellectual Property
- Life Sciences
- Materials
- Tech Scout
- Unparalleled Data Quality
- Higher Quality Content
- 60% Fewer Hallucinations
Browse by: Latest US Patents, China's latest patents, Technical Efficacy Thesaurus, Application Domain, Technology Topic, Popular Technical Reports.
© 2025 PatSnap. All rights reserved.Legal|Privacy policy|Modern Slavery Act Transparency Statement|Sitemap|About US| Contact US: help@patsnap.com