Method for improving metallization rate of metallurgical slag pellet
A metallization rate and metallurgical slag technology, applied in the field of metallurgy, can solve problems such as low iron content, low production efficiency, and long time, and achieve the effects of increasing metallization rate, increasing melting point, and promoting reduction
- Summary
- Abstract
- Description
- Claims
- Application Information
AI Technical Summary
Problems solved by technology
Method used
Image
Examples
Embodiment 1
[0054] Composition of copper smelting slag beneficiation tailings: iron content 38.75wt%, Cu content 0.26wt%, lead content 0.52wt%, zinc content 2.55wt%;
[0055] First, crush carbon black, anthracite, copper smelting slag beneficiation tailings, quicklime, slaked lime, magnesia and kaolin to a particle size of no more than 0.074mm, and then mix the mixture of carbon black, molasses and slaked lime in a pelletizer to make pellets , to obtain carbon-containing pellets with carbon black as the core, and then mix the carbon-containing pellets with copper smelting slag beneficiation tailings, anthracite, quicklime, molasses and slaked lime mixture in a pelletizer to obtain pellets containing Metallurgical slag pellets with carbon pellets as the core. Among them, the mass ratio of copper smelting slag beneficiation tailings: anthracite: quicklime: molasses: slaked lime in the smelting slag pellets is 100:22:10:5:3, and then it will contain magnesia The mixture of kaolin and metallu...
Embodiment 2
[0057] Composition of copper smelting slag beneficiation tailings: iron content 43.21wt%, Cu content 0.16wt%, lead content 0.26wt%, zinc content 1.09wt%;
[0058] Firstly crush coke powder, anthracite, copper smelting slag beneficiation tailings, quicklime, sodium carbonate, bentonite, magnesite and mullite to a particle size of not more than 0.074mm, and then mix the coke powder with bentonite and liquid binder Mix and pelletize in the pelletizing machine to obtain carbon-containing pellets with coke powder as the core, and then mix the carbon-containing pellets with copper smelting slag ore dressing tailings, anthracite, quicklime and sodium carbonate mixture, bentonite and liquid binder The mixture is mixed and pelletized in the pelletizer, so that the metallurgical slag pellets with carbon-containing pellets as the core can be obtained, among which, the copper smelting slag beneficiation tailings in the smelting slag pellets: anthracite: quicklime: sodium carbonate: bentoni...
Embodiment 3
[0060] Composition of nickel smelting slag: iron content 42.35%, Ni content 0.19%;
[0061]First crush graphite powder, coke powder, nickel smelting slag, sodium carbonate, bentonite and aluminum oxide to a particle size not greater than 0.074 mm, then mix graphite powder, bentonite and liquid binder in a pelletizer pelletizing to obtain carbon-containing pellets with graphite powder as the core, and then mix the carbon-containing pellets with copper smelting slag, beneficiation tailings, coke powder, sodium carbonate, bentonite and liquid binder mixture in a pelletizer Balls, so that the metallurgical slag pellets with carbon-containing pellets as the core can be obtained, wherein, nickel smelting slag: coke powder: sodium sulfate: bentonite: liquid binder = 100: 25: 6: 5: 10, and then three Aluminum oxide and metallurgical slag pellets are wrapped to form a high temperature resistant layer on the surface of the metallurgical slag pellets, thereby obtaining metallurgical slag...
PUM
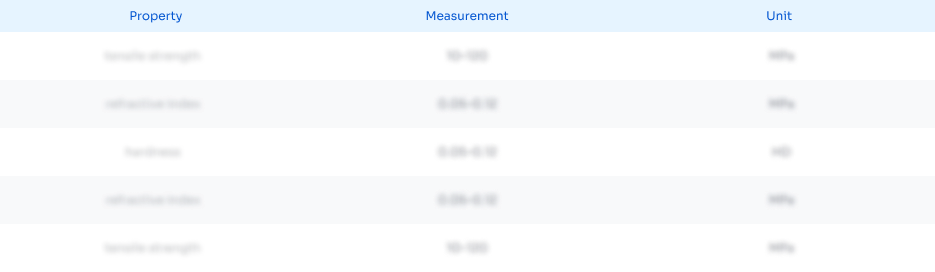
Abstract
Description
Claims
Application Information

- R&D Engineer
- R&D Manager
- IP Professional
- Industry Leading Data Capabilities
- Powerful AI technology
- Patent DNA Extraction
Browse by: Latest US Patents, China's latest patents, Technical Efficacy Thesaurus, Application Domain, Technology Topic, Popular Technical Reports.
© 2024 PatSnap. All rights reserved.Legal|Privacy policy|Modern Slavery Act Transparency Statement|Sitemap|About US| Contact US: help@patsnap.com