Vanadium titanium magnetite treatment device
A vanadium-titanium magnetite and processing device technology, applied in the field of metallurgy, can solve the problems of high cost and energy consumption, increase of process equipment, and low grade of titanium slag, so as to reduce production cost, reduce environmental pollution, and reduce production capacity consumption effect
- Summary
- Abstract
- Description
- Claims
- Application Information
AI Technical Summary
Problems solved by technology
Method used
Image
Examples
Embodiment 1
[0077]Take the vanadium-titanium magnetite rough ore with a medium iron grade of 12%, and obtain the vanadium-titanium magnetite concentrate with an iron grade of 32% after ore dressing; directly add the vanadium-titanium magnetite concentrate to the rotary kiln after mixing it with coal for 10 Carry out pre-reduction in, the weight of coal is 30% of vanadium-titanium-magnetite concentrate weight, the particle size of vanadium-titanium-magnetite concentrate is 4.2mm, the particle size of coal is 14.7mm, the temperature of pre-reduction in the rotary kiln 10 is 1100°C, the pre-reduction time is 7.0h. During the pre-reduction process, pelletized coal is injected into the kiln head of the rotary kiln 10 as fuel, and air is injected into the kiln body of the rotary kiln 10 to support combustion. The carbon monoxide produced by the combustion of pelletized coal The flow direction of the flue gas is opposite to the flow direction of the material. Finally, calcine and rotary kiln flue...
Embodiment 2
[0080] Take the vanadium-titanium magnetite coarse ore with a medium iron grade of 27%, and obtain the vanadium-titanium magnetite concentrate with an iron grade of 43% after ore dressing; directly add the vanadium-titanium magnetite concentrate to the rotary kiln after mixing it with coal for 10 Carry out pre-reduction, the weight of coal is 40% of vanadium-titanium magnetite concentrate weight, the particle size of vanadium-titanium magnetite concentrate is 4.7mm, the particle size of coal is 15.9mm, the temperature of pre-reduction in the rotary kiln 10 is 1200°C, the pre-reduction time is 5.1h. During the pre-reduction process, pelletized coal is injected into the kiln head of the rotary kiln 10 as fuel, and air is injected into the kiln body of the rotary kiln 10 to support combustion. The carbon monoxide and smoke produced by the pelletized coal combustion The flow direction of the gas is opposite to the flow direction of the material. Finally, calcine and rotary kiln flu...
Embodiment 3
[0083] Get the vanadium-titanium magnetite coarse ore that the middle iron grade is 38%, obtain the iron grade after ore dressing and be the vanadium-titanium magnetite concentrate of 59%, the particle size of the vanadium-titanium magnetite concentrate is 3.6mm; The iron ore concentrate is mixed with coal with a particle size of 18.8mm and directly added to the rotary kiln 10 for pre-reduction. The weight of the coal is 60% of the weight of the vanadium-titanium-magnetite concentrate, and the pre-reduction temperature in the rotary kiln 10 is 1300°C , the pre-reduction time is 2.0h. During the pre-reduction process, pelletized coal is injected into the kiln head of the rotary kiln 10 as fuel, and air is injected into the kiln body of the rotary kiln 10 to support combustion. The carbon monoxide and smoke produced by the pelletized coal combustion The flow direction of the gas is opposite to the flow direction of the material. Finally, calcine and rotary kiln flue gas with a me...
PUM
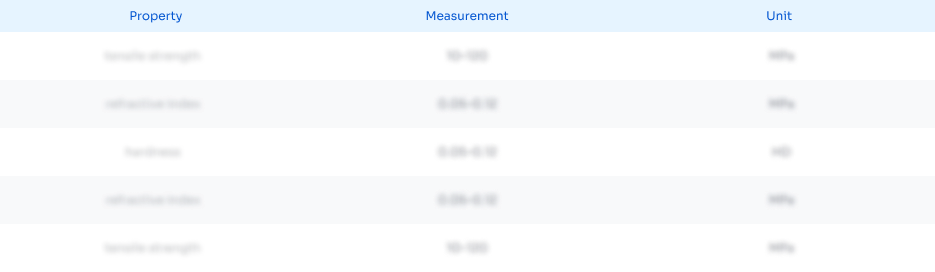
Abstract
Description
Claims
Application Information

- Generate Ideas
- Intellectual Property
- Life Sciences
- Materials
- Tech Scout
- Unparalleled Data Quality
- Higher Quality Content
- 60% Fewer Hallucinations
Browse by: Latest US Patents, China's latest patents, Technical Efficacy Thesaurus, Application Domain, Technology Topic, Popular Technical Reports.
© 2025 PatSnap. All rights reserved.Legal|Privacy policy|Modern Slavery Act Transparency Statement|Sitemap|About US| Contact US: help@patsnap.com