Chemical stainless steel polishing solution
A chemical polishing, stainless steel technology, applied in the field of metal surface treatment, can solve the problems of long pickling time, high temperature of pickling agent, pollution of the environment, etc., to improve the surface quality, enhance the pickling effect, and improve the stability.
- Summary
- Abstract
- Description
- Claims
- Application Information
AI Technical Summary
Problems solved by technology
Method used
Examples
Embodiment 1
[0019] In this embodiment 1, prepare 1L stainless steel polishing liquid according to the following method:
[0020] Measure 400 mL of water into the reaction kettle, slowly add 50 mL of concentrated sulfuric acid while stirring, after the temperature of the solution drops to room temperature, add 30 mL of ethanol, 15 g of urea, 20 g of citric acid, and 80 mL of nitric acid, 50 mL of phosphoric acid, 120 mL of hydrogen peroxide, and 150 mL of hydrofluoric acid were stirred evenly; finally, 2 g of hexamethylenetetramine, 0.5 g of sodium dodecylbenzenesulfonate and the rest of water were added to the reactor and stirred evenly to obtain Colorless and clear stainless steel chemical polishing solution.
Embodiment 2
[0022] In this embodiment 2, prepare 1L stainless steel polishing liquid according to the following method:
[0023] Measure 400 mL of water into the reaction kettle, slowly add 65 mL of concentrated sulfuric acid according to the formula while stirring, and after the temperature of the solution drops to room temperature, add 20 mL of ethanol, 10 g of urea, 30 g of citric acid, and 100 mL of nitric acid, 65 mL of phosphoric acid, 80 mL of hydrogen peroxide, and 120 mL of hydrofluoric acid were stirred evenly; finally, 4 g of hexamethylenetetramine, 1 g of sodium dodecylbenzenesulfonate and the rest of water were added to the reaction kettle and stirred Evenly, a colorless and clear stainless steel chemical polishing solution is obtained.
Embodiment 3
[0025] In this embodiment 3, prepare 1L stainless steel polishing liquid according to the following method:
[0026] Measure 400mL of water into the reaction kettle, slowly add 80mL of concentrated sulfuric acid according to the recipe while stirring, and after the temperature of the solution drops to room temperature, add 10mL of ethanol, 5g of urea, 40g of citric acid, and 120mL of Nitric acid, 80 mL of phosphoric acid, 50 mL of hydrogen peroxide, and 50 mL of hydrofluoric acid were stirred evenly; finally, 6 g of hexamethylenetetramine, 2 g of sodium dodecylbenzenesulfonate and the rest of water were added to the reactor and stirred evenly , to obtain a colorless and clear stainless steel chemical polishing solution.
PUM
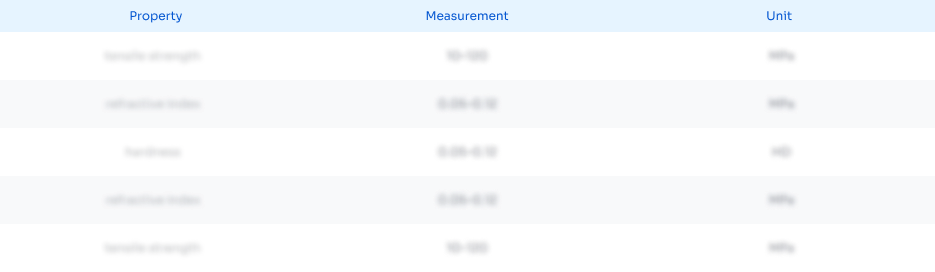
Abstract
Description
Claims
Application Information

- R&D Engineer
- R&D Manager
- IP Professional
- Industry Leading Data Capabilities
- Powerful AI technology
- Patent DNA Extraction
Browse by: Latest US Patents, China's latest patents, Technical Efficacy Thesaurus, Application Domain, Technology Topic, Popular Technical Reports.
© 2024 PatSnap. All rights reserved.Legal|Privacy policy|Modern Slavery Act Transparency Statement|Sitemap|About US| Contact US: help@patsnap.com