Preparation method of composite material and composite material
A technology of composite materials and mixtures, applied in the direction of graphene, nano-carbon, etc., can solve problems such as low strength, low surface hardness, and general mechanical properties
- Summary
- Abstract
- Description
- Claims
- Application Information
AI Technical Summary
Problems solved by technology
Method used
Examples
preparation example Construction
[0033] The preparation method of a kind of composite material of the present invention, comprises the following steps according to mass proportion:
[0034] a. Add 0.3-0.5 parts of single-layer graphene oxide to 79 parts of absolute ethanol, magnetically stir and then ultrasonically peel off; b. Add 100 parts of UHMWPE to the solution obtained through step a, magnetically stir again and then ultrasonically peel off; c. 1. Completely dry the mixture obtained in step b; d. Grind and pulverize the dried product after step c; e. After step d, use a flat vulcanizer to pre-press for 10-20min at a pressure of 5-10MPa; f. After the treatment in step e, hot air drying treatment; g. Vulcanization treatment and cooling.
Embodiment 1
[0036] The preparation method of a kind of composite material described in embodiment 1 of the present invention, comprises the following steps:
[0037] a. Add 0.3 gram of single-layer graphene oxide into 79 grams of absolute ethanol, stir magnetically at a speed of 150r / min for 2 hours, then place the stirred solution in an ultrasonic cleaning machine for ultrasonic peeling for 30 minutes; wherein absolute ethanol The specific gravity with water is calculated as 0.79, that is, 79ml of absolute ethanol;
[0038] b. Add 100 grams of UHMWPE to the solution obtained in step a, magnetically stir at a speed of 100 r / min for 1 hour, and then place it in an ultrasonic cleaning machine for ultrasonic peeling for 15 minutes;
[0039] c, place the mixture obtained through step b in a constant temperature water bath, and keep it warm at 60 degrees Celsius until it is completely dry;
[0040] d. Place the dry matter treated in step c in a ball mill and pulverize it at a speed of 300r / mi...
Embodiment 2
[0049]The preparation method of a kind of composite material described in embodiment 2 of the present invention, comprises the following steps according to mass gram ratio:
[0050] a. Add 0.4 gram of single-layer graphene oxide to 79 grams of absolute ethanol, stir magnetically at a speed of 160r / min for 2 hours, then place the stirred solution in an ultrasonic cleaning machine for ultrasonic peeling for 30 minutes; wherein absolute ethanol The specific gravity with water is calculated as 0.79, that is, 79ml of absolute ethanol;
[0051] b. Add 100 grams of UHMWPE to the solution obtained in step a, stir magnetically at a speed of 110 r / min for 1 hour, and then place it in an ultrasonic cleaning machine for ultrasonic peeling for 20 minutes;
[0052] c, place the mixture obtained through step b in a constant temperature water bath, and keep it warm at 60 degrees Celsius until it is completely dry;
[0053] d. Place the dry matter treated in step c in a ball mill and pulveriz...
PUM
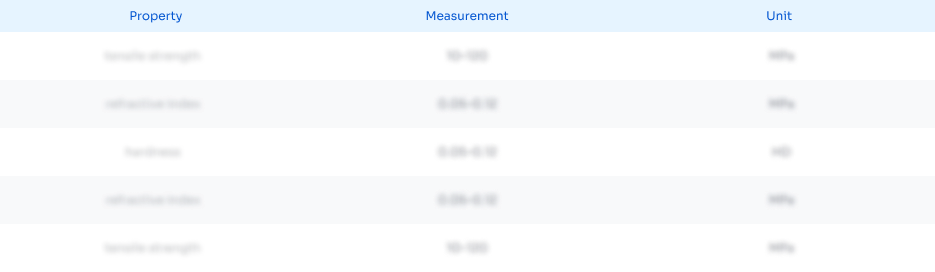
Abstract
Description
Claims
Application Information

- Generate Ideas
- Intellectual Property
- Life Sciences
- Materials
- Tech Scout
- Unparalleled Data Quality
- Higher Quality Content
- 60% Fewer Hallucinations
Browse by: Latest US Patents, China's latest patents, Technical Efficacy Thesaurus, Application Domain, Technology Topic, Popular Technical Reports.
© 2025 PatSnap. All rights reserved.Legal|Privacy policy|Modern Slavery Act Transparency Statement|Sitemap|About US| Contact US: help@patsnap.com