Nanometer modified SiO2/epoxy acrylic acid composite resin, IMD ink and preparation method thereof
A technology of epoxy acrylic and epoxy acrylate, which is applied in the direction of ink, household utensils, applications, etc., can solve the problems that cannot be met, and it is difficult to meet the performance requirements of high temperature resistance of 300 degrees, and achieve the effect of good flexibility
- Summary
- Abstract
- Description
- Claims
- Application Information
AI Technical Summary
Problems solved by technology
Method used
Image
Examples
Embodiment 1
[0024] First add 2g of deionized water, 4g of ammonia water and 100g of acetone solvent into a three-necked flask equipped with a condensation and electric stirrer device, and mix them uniformly at a speed of 300rpm, then mix 4g of tetraethyl orthosilicate and 50g of acetone solvent evenly Finally, drop it into a three-necked flask at a certain speed within 1 hour, and react at 70°C and 300rpm for 24h to obtain nano-SiO 2 Sol.
[0025] Mix 2g of vinyltriethoxysilane coupling agent with 50g of acetone solvent, and then add it dropwise to the above nano-SiO2 within 1 hour. 2 In the three-necked flask of the sol, the modified nano-SiO 2 Sol.
[0026] Add 0g, 6g, 18g, and 30g of nano-SiO to a four-necked flask equipped with a thermometer, a stirring device, a reflux condenser, and a dropping device. 2 sol, and heated to 80°C. Slowly drop 22g styrene, 9g butyl acrylate, 6.9g hydroxyethyl methacrylate, 8.5g epoxy acrylate and 0.93g azobisisobutyronitrile initiator into a four-ne...
Embodiment 2
[0027] Example 2 Nano SiO 2 / Preparation of epoxy acrylic polyurethane based IMD ink
[0028] The 30g nanometer SiO that embodiment 1 obtains 2 / epoxy acrylic resin (EPAc / SiO 2 (0%), EPAc / SiO 2 (1%), EPAc / SiO 2 (3%), EPAc / SiO 2 (5%)) as the main connection, respectively add curing agent 3.92g, 4.13g, 4.53g, 5.28gN3390 and 0.54g phthalic anhydride, 1g rosin phenolic resin 2104, 1g chlorinated polypropylene, 5g carbon black, 0.5 gBYK163, 0.1g BK-306, 0.1g BYK-141, add ethyl acetate until the total amount is 100g, and the solid content is 30%. According to the above proportions, after mixing the pigment, resin, wetting and dispersing agent, and solvent, use a Japanese Mitsubishi fine grinder to grind and disperse it for 1 hour to obtain a color paste, and then add quick-drying agent, adhesion promoter, leveling agent, Defoamer, curing agent, etc. are mixed and stirred evenly to obtain IMD ink, and EPAc / SiO 2 (0%), EPAc / SiO 2 (1%), EPAc / SiO 2 (3%), EPAc / SiO 2 (5%)) are...
Embodiment 3
[0029] Example 3 Nano SiO 2 / Epoxy acrylic polyurethane based IMD ink properties
[0030]The heat resistance of the ink film refers to the national standard GB / T 1735 "Determination of Heat Resistance of Paint Film". The heat resistance of the paint film refers to the ability of the paint film to maintain its apparent state or mechanical properties at a given temperature, using a muffle furnace After heating and reaching the specified temperature and time, the heat resistance of the paint film can be expressed by the change of physical properties or the change of the surface of the paint film. In this experiment, the heat resistance of the ink film is represented by the time when the ink film does not suffer from wrinkling, bubbling, cracking or discoloration at 300°C. The hardness of the coating film is measured with reference to the national standard GB / T 6739-1996 "Pencil Test Method for Coating Film Hardness". It is divided into 13 grades from 6H to 6B, of which 6H is th...
PUM
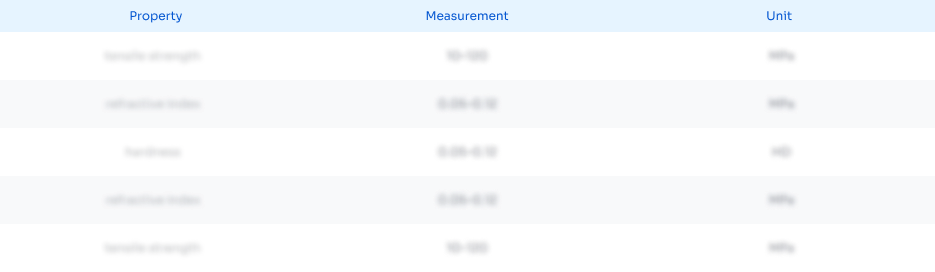
Abstract
Description
Claims
Application Information

- R&D
- Intellectual Property
- Life Sciences
- Materials
- Tech Scout
- Unparalleled Data Quality
- Higher Quality Content
- 60% Fewer Hallucinations
Browse by: Latest US Patents, China's latest patents, Technical Efficacy Thesaurus, Application Domain, Technology Topic, Popular Technical Reports.
© 2025 PatSnap. All rights reserved.Legal|Privacy policy|Modern Slavery Act Transparency Statement|Sitemap|About US| Contact US: help@patsnap.com