A kind of preparation method of solid acrylic resin
A solid acrylic and resin technology, applied in applications, inks, household appliances, etc., can solve the problems of high pressure, high temperature, and the temperature of solid acrylic resin is difficult to control, so as to improve the conversion rate, overcome the difficult control of polymerization temperature, and eliminate residual single body effect
- Summary
- Abstract
- Description
- Claims
- Application Information
AI Technical Summary
Problems solved by technology
Method used
Image
Examples
Embodiment 1
[0029] See figure 1 . Add 20 kg of styrene, 40 kg of ethyl acrylate, 5 kg of methacrylonitrile, 3 kg of benzoyl peroxide, 1 kg of thioglycolic acid, and 20 kg of polyurethane into the material tank 1, stir and dissolve After uniformity, put it into the reactor 2 at one time, raise the temperature from room temperature to 120°C, and carry out the polymerization reaction at 0.1MPa; during the reaction, the total conversion rate of the above-mentioned monomers is continuously monitored. When the total conversion rate of the above-mentioned monomers in the reactor is When the rate was 40%, 11 kilograms of ethylene glycol butyl ether acetates were gradually dripped into the reactor from the solvent storage tank 8 and carried out viscosity reduction, so that the material in the reactor was kept in a good flow state all the time until After making the total conversion of the above-mentioned monomers reach 70%, the resulting dilution is discharged from the reactor 2 into the storage ...
Embodiment 2
[0031] See figure 1. 55 kg of α-methylstyrene, 10 kg of butyl acrylate, 3 kg of 2-hydroxyethyl acrylate, 2 kg of maleic acid, 1 kg of dilauroyl peroxide, 2.75 kg of 3- Add mercaptopropionic acid, 10 kg of alkyd resin, and 2.5 kg of tertoctyl phenolic resin into the material tank 1, stir and dissolve evenly, and put it into the reactor 2 at one time, raise the temperature from room temperature to 180 ° C, and carry out polymerization reaction at 1 MPa During the reaction, constantly monitor the total conversion rate of the above-mentioned monomers, when the total conversion rate of the above-mentioned monomers in the reactor 2 was 50%, start to gradually drop 13.75 kilograms of propylene glycol methyl ether into the solvent storage tank 8 Viscosity reduction is carried out in the reactor 2, so that the material in the reactor 2 is kept in a good flow state all the time, until the total conversion rate of the above-mentioned monomers reaches 80%, the gained dilution is discharg...
Embodiment 3
[0033] See figure 1 . 20 kg of benzyl acrylate, 17.5 kg of benzyl methacrylate, 20 kg of ethyl acrylate, 5 kg of 2-ethylhexyl acrylate, 5 kg of glycidyl acrylate, 5 kg of acrylic acid, 7.5 kg of 4-pentene-1,2,3,4-tetracarboxylic acid, 0.5 kg of tert-amyl peroxy-2-ethylhexanoate, 3 kg of butyl 3-mercaptopropionate, 5 kg of polyphenylene Ether and 6.5 kg of polysulfone were added to the material tank 1, stirred and dissolved evenly, and then put into the reactor 2 at one time, and the temperature was raised from room temperature to 160 ° C, and the polymerization reaction was carried out at 0.7 MPa; during the reaction, the above-mentioned monomers were continuously monitored. Total conversion rate, when the total conversion rate of the above-mentioned monomers in the reactor 2 was 45%, the propylene glycol methyl ether acetate of 1 kilogram, the propylene glycol ethyl ether propionate of 4 kilograms were gradually dripped from the solvent storage tank 8 into the reactor 2 for...
PUM
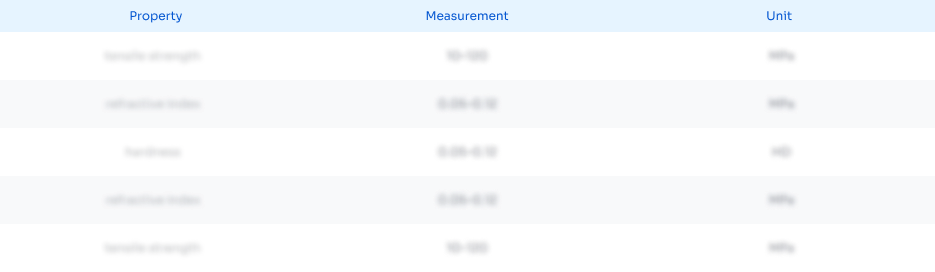
Abstract
Description
Claims
Application Information

- R&D
- Intellectual Property
- Life Sciences
- Materials
- Tech Scout
- Unparalleled Data Quality
- Higher Quality Content
- 60% Fewer Hallucinations
Browse by: Latest US Patents, China's latest patents, Technical Efficacy Thesaurus, Application Domain, Technology Topic, Popular Technical Reports.
© 2025 PatSnap. All rights reserved.Legal|Privacy policy|Modern Slavery Act Transparency Statement|Sitemap|About US| Contact US: help@patsnap.com