Boride hardfacing flux-cored wire and preparation method thereof
A technology of boride and flux, which is applied in the field of boride wear-resistant surfacing flux-cored welding wire and its preparation, can solve the problems of poor weldability, poor corrosion resistance, and low bonding strength, and achieve reduced preparation costs and corrosion resistance. Good, solderability-enhancing effect
- Summary
- Abstract
- Description
- Claims
- Application Information
AI Technical Summary
Problems solved by technology
Method used
Image
Examples
Embodiment 1
[0019] A boride wear-resistant surfacing flux-cored welding wire and a preparation method thereof. The preparation method described in this embodiment is as follows: firstly dry the flux core, mix it evenly; then put it into the sheath, and draw it to obtain the boride wear-resistant surfacing flux-cored welding wire.
[0020] The outer skin described in this embodiment is common low carbon steel.
[0021] The composition and content of the drug core described in this embodiment are: B is 1~4wt%, Mo is 25~40wt%, Ni is 9~12wt%, Cr is 15~20wt%, C is 0.2~2wt%, and the balance For Fe.
Embodiment 2
[0023] A boride wear-resistant surfacing flux-cored welding wire and a preparation method thereof. The preparation method described in this embodiment is as follows: firstly dry the flux core, mix it evenly; then put it into the sheath, and draw it to obtain the boride wear-resistant surfacing flux-cored welding wire.
[0024] The outer skin described in this embodiment is stainless steel.
[0025] The composition and content of the drug core described in this embodiment are: B is 3~6wt%, Mo is 35~50wt%, Ni is 7~9wt%, Cr is 10~16wt%, C is 0.2~2wt%, and the balance For Fe.
Embodiment 3
[0027] A boride wear-resistant surfacing flux-cored welding wire and a preparation method thereof. The preparation method described in this embodiment is as follows: firstly dry the flux core, mix it evenly; then put it into the sheath, and draw it to obtain the boride wear-resistant surfacing flux-cored welding wire.
[0028] The outer skin described in this embodiment is common low carbon steel.
[0029] The composition and content of the drug core described in this embodiment are: B is 5~8wt%, Mo is 45~60wt%, Ni is 5~8wt%, Cr is 5~10wt%, C is 0.2~2wt%, and the balance For Fe.
PUM
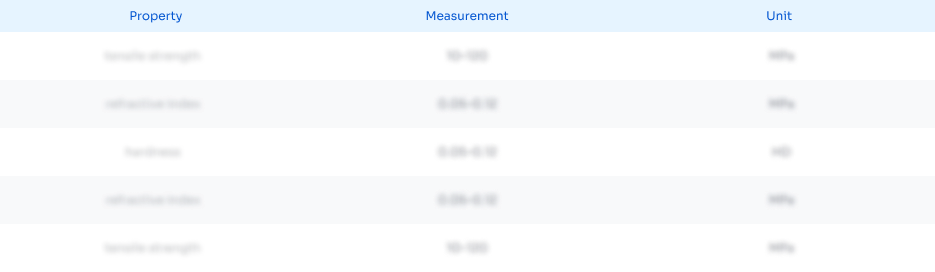
Abstract
Description
Claims
Application Information

- R&D Engineer
- R&D Manager
- IP Professional
- Industry Leading Data Capabilities
- Powerful AI technology
- Patent DNA Extraction
Browse by: Latest US Patents, China's latest patents, Technical Efficacy Thesaurus, Application Domain, Technology Topic, Popular Technical Reports.
© 2024 PatSnap. All rights reserved.Legal|Privacy policy|Modern Slavery Act Transparency Statement|Sitemap|About US| Contact US: help@patsnap.com