Molybdenum oxide ores composite pellets used for argon oxygen refining furnace and preparation method thereof
An argon-oxygen refining furnace and molybdenum oxide ore technology, which is applied in the field of composite pellets, can solve the problems of high temperature in the electrode area, intensified volatilization of molybdenum oxide, and poor reduction kinetic conditions.
- Summary
- Abstract
- Description
- Claims
- Application Information
AI Technical Summary
Problems solved by technology
Method used
Image
Examples
Embodiment 1-8
[0044] In the smelting process of the argon-oxygen refining furnace, before loading the stainless steel mother liquor, lime and lightly burned dolomite of 1 / 3 of the total amount of slag are added, and after igniting and blowing for 2 minutes, the molybdenum oxide ore composite pellets of the present invention are added from the furnace top silo , using the side blowing and strong stirring function of the argon-oxygen refining furnace to make it fully react with the hot metal, a small part of molybdenum oxide that has not undergone reduction reaction, and calcium oxide form calcium molybdate and enter the slag.
[0045] The composition of embodiment 1-8 is referring to table 3:
[0046] Table 3: Molybdenum Oxide Composite Pellet Ratio of Each Component
[0047]
[0048] In the argon-oxygen refining furnace with a nominal capacity of 120 tons, the steel type is stainless steel 316L, the process path adopts the electric furnace + AOD + VOD method, the mother liquor [C] of the...
PUM
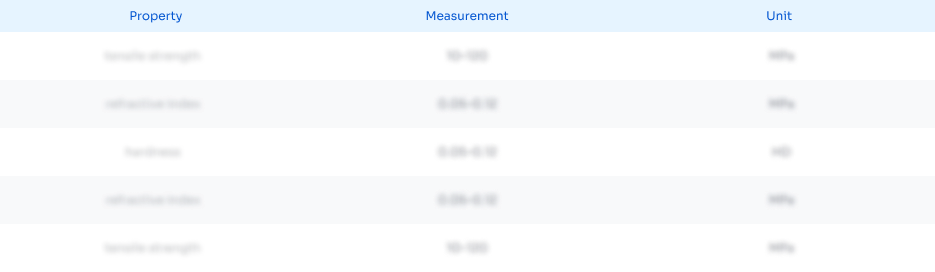
Abstract
Description
Claims
Application Information

- Generate Ideas
- Intellectual Property
- Life Sciences
- Materials
- Tech Scout
- Unparalleled Data Quality
- Higher Quality Content
- 60% Fewer Hallucinations
Browse by: Latest US Patents, China's latest patents, Technical Efficacy Thesaurus, Application Domain, Technology Topic, Popular Technical Reports.
© 2025 PatSnap. All rights reserved.Legal|Privacy policy|Modern Slavery Act Transparency Statement|Sitemap|About US| Contact US: help@patsnap.com