Gasoline engine piston material and preparation method thereof
A gasoline engine and piston technology, applied in the field of gasoline engine piston materials and their preparation, can solve the problems that the performance cannot meet the high strength requirements of a supercharged direct injection piston, the ability to withstand high temperature loads cannot meet the requirements, and the high temperature resistance strength of the piston is poor. Achieve good machinability and mechanical properties, low cost, improve high temperature strength and high temperature thermal stability
- Summary
- Abstract
- Description
- Claims
- Application Information
AI Technical Summary
Problems solved by technology
Method used
Examples
preparation example Construction
[0050] A preparation method of a gasoline engine piston material, comprising the following steps:
[0051] 1) Add aluminum ingots according to the weight percentage in the melting furnace, heat to 580-600 ° C, the aluminum ingots are melted, add L-type low-temperature slag remover with 0.2-0.3% of the weight of the aluminum ingots, stir to remove surface impurities, and remove the impurities except AL Add Si, Fe, Cu, Mn, Mg, Ni, Zn, Ti, Pb into the melting furnace according to their respective weight percentages, continue heating until the above metals are completely melted, and then add H-type slag removal with 0.2-0.3% of the weight of the aluminum ingot agent;
[0052] 2) Transfer the molten aluminum into the holding furnace and keep it warm at 740-770 ℃, add phosphorus compound modifier with 0.2-0.3% of the weight of the aluminum ingot for refinement and modification;
[0053] 3) Add 0.1-0.2% high-temperature slag remover by weight of aluminum ingot to the melted molten a...
Embodiment 1
[0059] 1) Add 79.65kg aluminum ingot to the smelting furnace, heat to 580-600°C, melt the aluminum ingot, add L-type low-temperature slag remover with 0.2% of the weight of the aluminum ingot, stir to remove surface impurities, and remove 12.5kg of Si except AL , Fe 0.2kg, Cu 5.3kg, Mn 0.1kg, Mg 1.0kg, Ni 1.0kg, Zn 0.1kg, Ti 0.1kg, Pb 0.05kg into the melting furnace, continue to heat until the above metals are completely melted, and then add aluminum ingots 0.2% by weight of H-type slag remover;
[0060] 2) Transfer the above-mentioned molten aluminum liquid into the holding furnace and keep it warm at 740-770°C, and add a phosphorus compound modifier of 0.2% by weight of the aluminum ingot for refinement and modification;
[0061] 3) Add 0.2% high-temperature slag remover by weight of the aluminum ingot to the melted molten aluminum after the refinement and deterioration treatment above for slag removal treatment, stir the liquid surface for degassing for 13-16 minutes, and t...
Embodiment 2
[0068] 1) Add 79.45kg of aluminum ingot to the melting furnace, heat to 580-600°C, melt the aluminum ingot, add L-type low-temperature slag remover with 0.3% of the weight of the aluminum ingot, stir to remove surface impurities, put 12kg of Si except AL, Add Fe 0.3kg, Cu 5.8kg, Mn 0.2kg, Mg 1.3kg, Ni 0.8kg, Zn 0.05kg, Ti 0.05kg, Pb 0.05kg into the melting furnace, continue to heat until the above metals are completely melted, and then add the weight of aluminum ingots 0.3% H-type slag remover;
[0069] 2) Transfer the above-mentioned molten aluminum liquid into the holding furnace and keep it warm at 740-770°C, and add a phosphorus compound modifier of 0.3% by weight of the aluminum ingot for refinement and modification;
[0070] 3) Add a high-temperature slag remover of 0.1% by weight of the aluminum ingot to the molten aluminum after the refinement and deterioration treatment above for slag removal treatment, stir the liquid surface and perform degassing for 13-16 minutes, ...
PUM
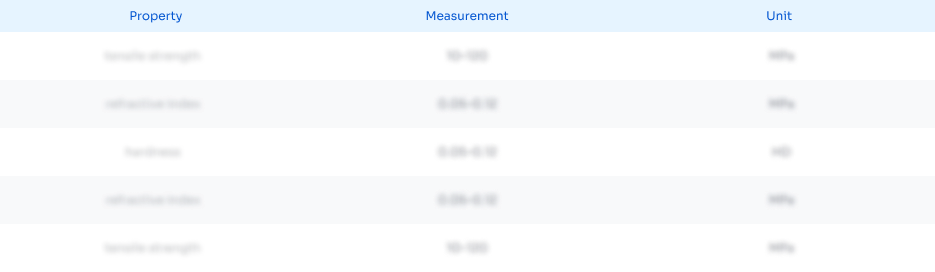
Abstract
Description
Claims
Application Information

- R&D Engineer
- R&D Manager
- IP Professional
- Industry Leading Data Capabilities
- Powerful AI technology
- Patent DNA Extraction
Browse by: Latest US Patents, China's latest patents, Technical Efficacy Thesaurus, Application Domain, Technology Topic, Popular Technical Reports.
© 2024 PatSnap. All rights reserved.Legal|Privacy policy|Modern Slavery Act Transparency Statement|Sitemap|About US| Contact US: help@patsnap.com