Agitation friction point braze welding method for metal plate overlap joint combination
A friction stir, metal sheet technology, applied in metal processing equipment, welding equipment, welding equipment and other directions, can solve the problems of complex tool design and preparation, demanding power supply capacity, limited welding area, etc., to achieve excellent film removal ability, eliminate Brittle crystal structure and cracks, the effect of simplifying tool design and manufacture
- Summary
- Abstract
- Description
- Claims
- Application Information
AI Technical Summary
Problems solved by technology
Method used
Image
Examples
Embodiment Construction
[0033] The present invention will be described in detail below in conjunction with the accompanying drawings and embodiments.
[0034] The applicant aimed at the common problems (limited welding area; needle wear) and special problems (residual keyhole; complex tool design and manufacture) existing in the existing friction stir spot welding technology, by using needle-free tools, pre-set solder and increasing the top In the forging process, a friction stir spot brazing technology (FSSB: Friction Stir Spot Brazing) using a needle-free tool is proposed to obtain a dense interface, no brittle crystal structure, no keyhole, no wear, a large area, high efficiency, and energy saving. welding effect. The basic process (including tools and solder) see figure 1 (a) ~ (d). However, if the upper plate of the spot welding combination is a thick plate (thickness greater than or equal to 5mm), considering that the strength of the stress and strain field transmitted to the welding interfac...
PUM
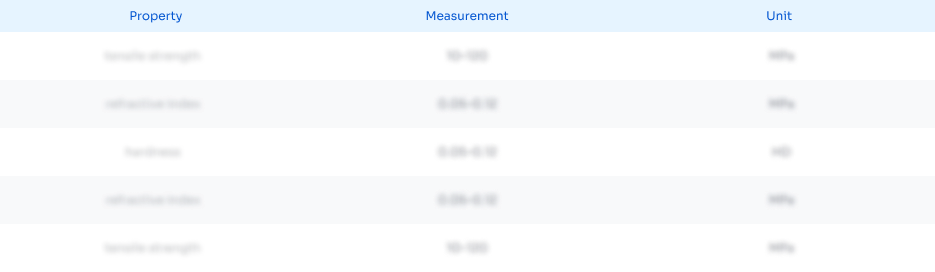
Abstract
Description
Claims
Application Information

- Generate Ideas
- Intellectual Property
- Life Sciences
- Materials
- Tech Scout
- Unparalleled Data Quality
- Higher Quality Content
- 60% Fewer Hallucinations
Browse by: Latest US Patents, China's latest patents, Technical Efficacy Thesaurus, Application Domain, Technology Topic, Popular Technical Reports.
© 2025 PatSnap. All rights reserved.Legal|Privacy policy|Modern Slavery Act Transparency Statement|Sitemap|About US| Contact US: help@patsnap.com